Lab safety
The EHSO Lab Safety program provides supports for labs as well as hazard-specific programs including the Biosafety Program, Animal Care Occupational Health, and Radiation Safety Program.
This includes the following sections:
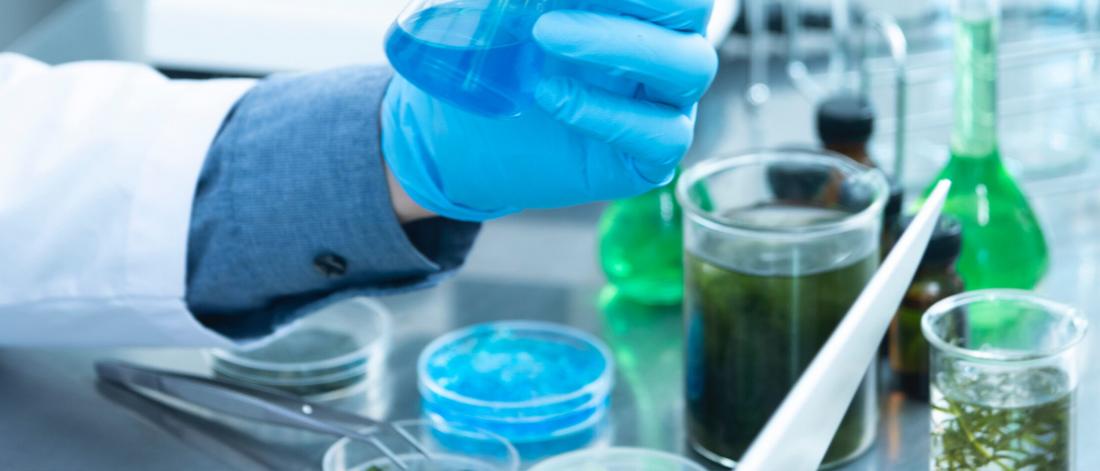
Lab safety
Lab permits
A lab is a room or area that contains hazardous materials subject to EHSO permitting for the purpose of teaching or research. This includes X-ray rooms, workshops, storage areas, and research and instructional laboratories.
To be subject to EHSO permitting, your activities must meet one of the following requirements:
- Biosafety permit - required to work with biological agents.
- Radiation safety permits - required to work with radioactive material or X-Ray equipment.
- Chemical safety permit - required for rooms or work that meet(s) threshold quantities of chemicals.
More information on each type of permit is found within each section below.
EHSO permit application and management activities occur using the EHSA database.
Biosafety program
The University of Manitoba’s Biosafety Program is in place to ensure the UM operates in compliance with the requirements of all related biosafety legislation as well as to ensure the safety of the UM Community. More information can be found on the Biosafety page.
Animal care occupational health program
The University of Manitoba’s Animal Care Occupational Health Program supports animal care workers, researchers, and technicians working with animals for research purposes. More information can be found on the Animal Care Occupational Health page.
Radiation safety program
The University of Manitoba’s Radiation Safety Program ensures work with radioisotopes, x-ray equipment and lasers occurs in adherence with municipal, provincial and federal regulations. This type of work occurs across many areas at the University. This is reflected in the diverse membership of the UM Radiation Protection Committee supporting this program with its expertise.
More information can be found on the UM Radiation Safety page. Please contact UM Radiation Safety with all program related inquiries.
Chemical safety program
The Chemical Safety Program ensures the safe and knowledgeable use of chemicals at the University of Manitoba, whether in the workplace, lab, or classroom. To find information on WHMIS, chemical inventories, storage and handling, chemical waste, chemical safety permits, spill response and post exposure protocols for chemicals, visit the Chemical Safety page.
If you have any questions regarding chemicals, contact us at chemsafe@umanitoba.ca.
Lab signage
All permitted lab spaces must have a Workplace Hazardous Information Placard (WHIP) posted on the door. This placard identifies personal protective equipment (PPE) that are required for entry into the lab, hazards that are present in the lab space, and contact information for the supervisors in charge of the lab space. A WHIP is generated from the permitted hazards specific to a lab space and can be printed directly from EHSA. For information on how to update your WHIPS, please visit the Lab Safety UM Intranet page.
The following lab posters are for reference and will be located in labs where their information applies. These posters will be provided by EHSO and are not required to be printed from this site.
Lab personal protective equipment
A lab has two levels of personal protective equipment (PPE) requirements, entry level requirements which are designated on the lab door and task-specific personal protective equipment, which are communicated through safe work procedures and lab-specific training. Information on different types of PPE, including gloves, safety eyewear, respiratory protection, and safety footwear, can be found here.
Lab coats
Lab coats are a commonly required protective layer in many lab spaces. They are worn to protect your clothes and skin from contamination by hazardous products and must be removed when leaving a containment zone or lab area.
Lab coats should:
- Have quick release fastenings (i.e. snaps) and close-fitting cuffs
- Be knee-length
- Be made of flame-retardant material
Laundering Services
The University of Manitoba has a list of preferred suppliers that can be used for laundering services.
Please contact the below suppliers for a quote. This will need to be uploaded into EPIC. For further questions/assistance with purchasing or laundering lab coats contact purchasing@umanitoba.ca.
- Canadian Linen & Uniform Services – (Vendor #007642220)
- Phone: 204-480-5561 / canadianlinen.ca
- Dollarwise Quality Cleaners – (Vendor #007735292)
- Phone: 204-452-8166 / drycleangreen.ca
- Perth’s – (Vendor #007728511)
- Phone: 204-697-6100 / perths.ca
- Quintex Services Ltd. – (Vendor #007706789)
- Phone: 204-477-6600 / quintexservices.com
Lab safety training
Safety training consists of both formal courses offered through UMLearn and task-specific training that will be offered through the lab. Use the Lab Safety Training Checklist for New Lab Workers (PDF) to ensure workers in the lab are fully trained before starting their work.
Lab equipment
Some of the specialty equipment in labs require additional monitoring and safety requirements. Guides and other documentation are available for users on the UM Intranet, including information for the following:
- Fume Hoods
- Incinerators
- Autoclaves and Biological Safety Devices
- Emergency Showers and Eyewash Stations
- Radiation Safety Devices
For information regarding equipment used for chemical storage such as chemical safety cabinets (i.e. flammable cabinets), refrigerators, or freezers, please see Chemical Storage on the Chemical Safety page.
Any equipment used with hazardous products (chemical, biological or radiological) must be decontaminated prior to disposal or having maintenance conducted by Physical Plant. Decontamination of lab equipment is the responsibility of the equipment owner, who may delegate that work to the person or department using the equipment.
Servicing lab equipment in the lab
The Hazard Clearance Form needs to be completed for any equipment to be serviced in the lab by non-lab staff. Send the form to EHSO when the equipment is ready, and we will schedule an inspection with you to confirm and provide a sign-off. Include the completed form when submitting a maintenance request with Physical Plant.
Disposing of lab equipment or servicing outside the lab
The Lab Equipment Decommissioning Form needs to be completed for any equipment that leaves the lab. Send the form to EHSO when the equipment is ready, and we will schedule an inspection with you to confirm and provide a sign-off and attach appropriate identification to the equipment. Include the completed form when submitting for disposal of capital assets with Finance or submitting a maintenance request with Physical Plant to have the equipment relocated.
Once lab equipment has been appropriately decontaminated, it can be disposed of as regular waste. This could include recycling, landfill, scrap metal, or selling or donating to another lab.
Note: This includes disposal of fridges or freezers used for chemical or lab sample storage.
Lab waste disposal
The lab waste disposal guide is a guide for the proper disposal of laboratory materials at the University of Manitoba. It outlines disposal requirements at federal, provincial, and municipal levels to protect people and the environment. Proper waste handling ensures safety for lab workers and waste collection staff. The guide summarizes Lab Safety Program requirements and references relevant procedures. It also accompanies the EHSO Lab Waste Disposal Chart, a mandatory poster for all campus labs.
Lab design, decommissioning, and hazard clearance
Activities involving lab design, whole room decommissioning, lab hazard clearance or decommissioning of lab equipment may only be undertaken by technically qualified persons. The signatory on the forms must be someone with technical knowledge and a significant level of responsibility in the lab. Under no circumstances may administrative staff be tasked with these duties.
Designing a lab
Environment, health and safety considerations are included from the very beginning of design stages for new and renovated lab spaces. If you are planning to develop a new lab or renovating an existing lab, submit your project request to Architectural and Engineering Services (AES). Complete and provide the Design Review Form with your project request to help assess the hazards in the lab and identify the safety needs for the space.
Lab Safety- Design Review Procedure (PDF)
Lab Safety- EHS Review Form (PDF)
Please visit Architectural and Engineering Services (AES)site to submit your project request
Once your lab design project is approved to proceed, AES will provide your form to the Environmental Health and Safety Office (EHSO) to review design requirements to be sent to the designer and included in the plans. EHSO will contact the lab owner if there are any questions or to further discuss your needs.
Lab Safety- EHS Design Requirements (PDF)
Lab Safety- EHS Design Checklist (PDF)
A resource document is provided to assist in acquiring safety equipment, signage, and other safety resources that apply to labs at the UM. This can be helpful in the design of a new lab or a lab renovation or simply to refresh or verify safety resources.
Decommissioning a lab
Whole room decommissioning is required for labs prior to any major renovation, change of use, or transition to a different researcher. This is required for any area where Hazardous Materials (chemical, biological or radiological) are used or stored.
Decommissioning is the responsibility of the permit holder, and tasks may be delegated to the person(s) using the space.
Lab Decommissioning Form (PDF)
For lab equipment that needs to be decommissioned, complete a Lab Equipment Decommissioning Form.
Performing maintenance in a lab
Labs or storage areas where hazardous materials (chemical, biological or radiological) are used or stored must be cleared of hazards prior to maintenance or service activities. Complete a Lab Hazard Clearance Form, then request an inspection from EHSO to confirm and provide sign-off. A completed form is required when submitting a Work Request with Physical Plant.
Lab chairs and furnishings
For lab use, chairs should be non-porous and non-absorbent, easy to clean, and resistant to physical damage caused by decontamination procedures. Non-absorbent materials may include stainless steel, epoxy resin, or chemical-resistant plastic laminate for benchtops, and urethane or vinyl for stools and chairs. These materials will ensure that in the event of a spill, liquids won’t soak in or lie in crevices in the back and seat. Lab users must be able to collect any hazardous liquid with an absorbent, wash with an appropriate cleaner or disinfectant and enable the chair to be continually used in a safe manner.
This information promotes safe work practices with all lab hazards, but it is best referenced in the Canadian Biosafety Standard, section 3.3.
Lab safety inspections
According to the Manitoba Workplace Safety and Health Act and Regulation, all workplace facilities require annual safety inspections to identify hazards. The purpose of these inspections is to proactively mitigate the risk of hazards in order to prevent an incident or injury. The laboratories of the University of Manitoba are inspected by members of the Environmental Health and Safety Office, whose programs help to promote a safe working and learning environment within our laboratories. The inspection criteria are derived from EHS legislation as established by EHS programs and approved through the various safety and health committees.
Review the Lab Safety – General Inspection Procedure document posted on this site to learn more.
Environmental Health and Safety Assistant database
Permits for the use of chemicals and biological agents in lab spaces are administered through the Environmental Health and Safety Assistant (EHSA) database. To apply for a new lab permit and manage existing permits including items regarding lab workers, training, hazardous materials, and inspection findings, log into EHSA using your UMNetID and password.
Log in to EHSA Request access to EHSA
Instructional materials are available on the UM Intranet to aid you in common tasks including initial applications, submitting permit amendments, viewing lab inspection results, and closing corrective actions.
Ancillary workers
University employees who do not regularly work in the lab may be required on occasion to work in lab spaces in various facility support roles. This affects employees, such as those in Information Services and Technology (IST), Operations & Maintenance, and Caretaking. Training is available for ancillary workers to ensure they are able to identify hazards and assess risks in order to work safely in a specialized environment. Lab Safety for Non-Lab Workers can be found in UM Learn as an online course for self-registration.
Visitors to the labs
Visitors to a lab include any person who is not a student or employee of the University of Manitoba. Visitors are required to follow all safety requirements, including donning of personal protective equipment for entry and/or work within these spaces.
Refer to the requirements for hosting a visitor, as outlined on the Hosting a Visitor section of the Visitor Safety page.
You may also be looking for
Contact us
Environmental Health and Safety
Room 191 Extended Education Complex
406 University Crescent
University of Manitoba (Fort Garry campus)
Winnipeg, MB R3T 2N2 Canada
P310 Pathology Building
770 Bannatyne Avenue
University of Manitoba (Bannatyne Campus)