Faculty of Architecture
Projects/Research
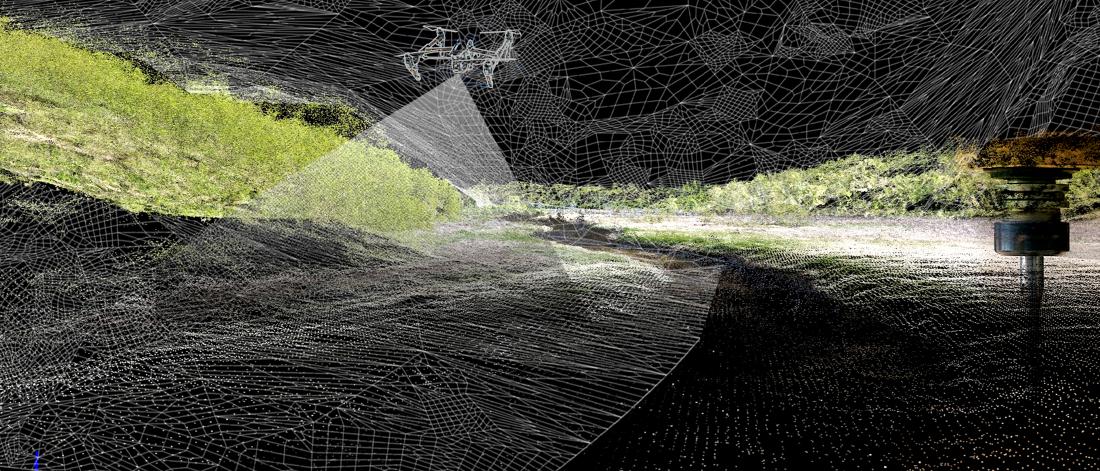
FABLab
Made In House
The hewn tree
The decimated rock
The sheep shorn hair
All hold expression of time, intent, value and meaning in their material being
The hand. The eye. The mind
The tool. The focus. The time
Together bring expression to a collective material body
“Technique has a bad name; it can seem soulless. That’s not how people whose hands become highly trained view technique. For them, technique will be intimately linked to expression.” - Richard Sennet
‘Made in House’, is a collection of work that has been enacted by faculty and students, by way of physical support and embodied material knowledge. This work surveys the technical and material capacity of the FAUM facilities, and asks the question; what deeper knowledge can be gained from the dedicated pursuit of technique and craft?
FABLab + Workshop + C.A.S.T.
Benita Kliewer
Lancelot Coar
Kellen Deighton
Jeramee Fajardo
Jason Hare
Karen Hare
Tijen Roshko
Jon Watts
FABLab + Workshop + C.A.S.T.
Benita Kliewer
Lancelot Coar
Kellen Deighton
Jeramee Fajardo
Jason Hare
Karen Hare
Tijen Roshko
Jon Watts
FABLab + Workshop + C.A.S.T.
Benita Kliewer
Lancelot Coar
Kellen Deighton
Jeramee Fajardo
Jason Hare
Karen Hare
Tijen Roshko
Jon Watts
FABLab + Workshop + C.A.S.T.
Benita Kliewer
Lancelot Coar
Kellen Deighton
Jeramee Fajardo
Jason Hare
Karen Hare
Tijen Roshko
Jon Watts
FABLab + Workshop + C.A.S.T.
Benita Kliewer
Lancelot Coar
Kellen Deighton
Jeramee Fajardo
Jason Hare
Karen Hare
Tijen Roshko
Jon Watts
FABLab + Workshop + C.A.S.T.
Benita Kliewer
Lancelot Coar
Kellen Deighton
Jeramee Fajardo
Jason Hare
Karen Hare
Tijen Roshko
Jon Watts
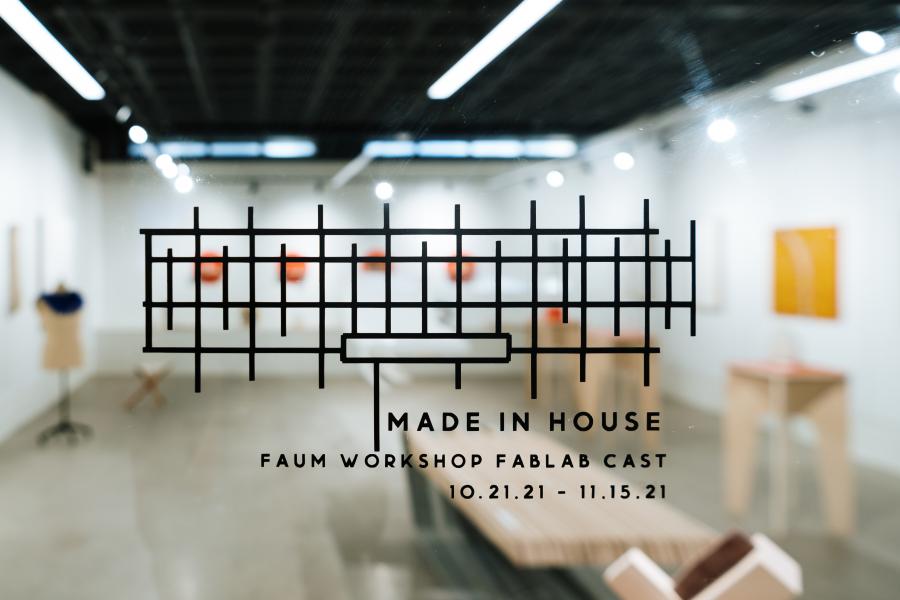
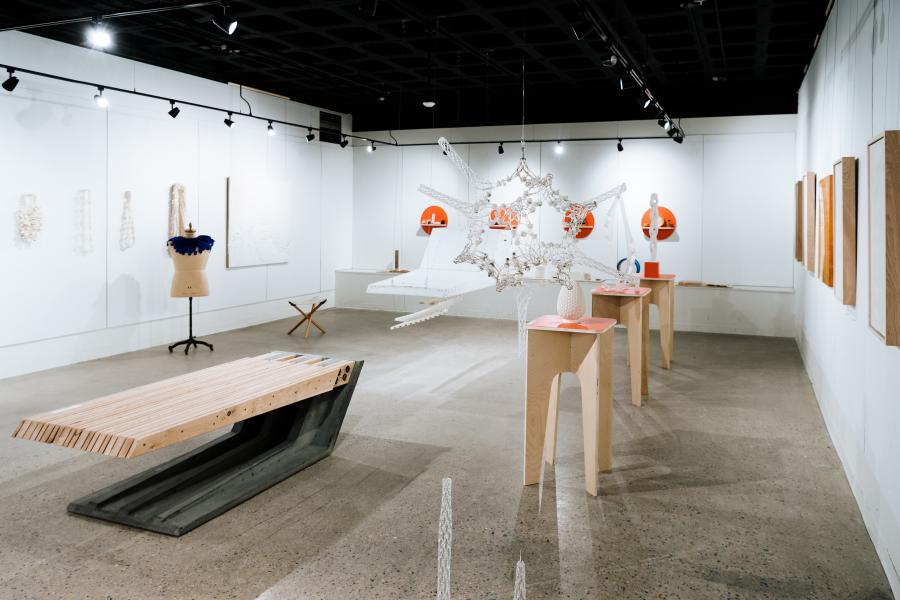
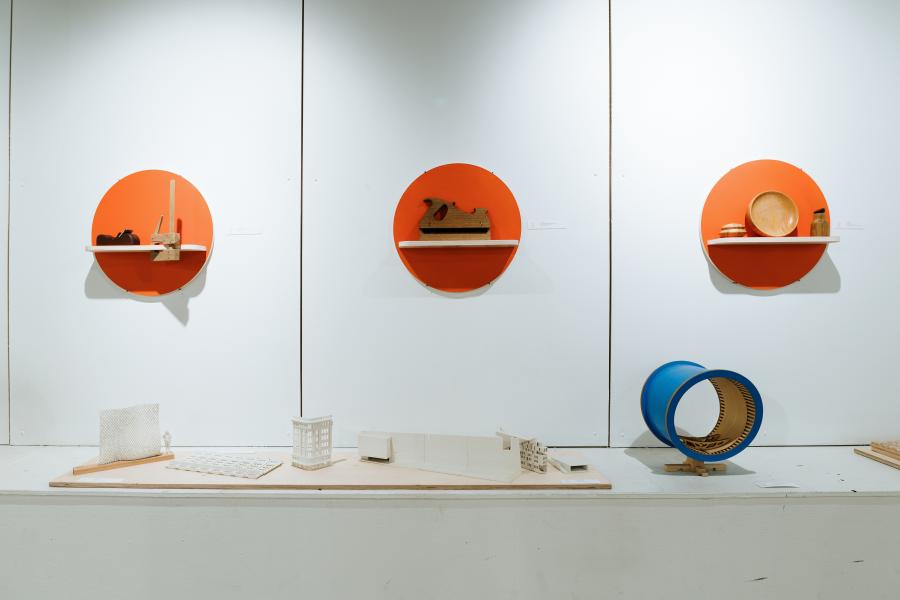
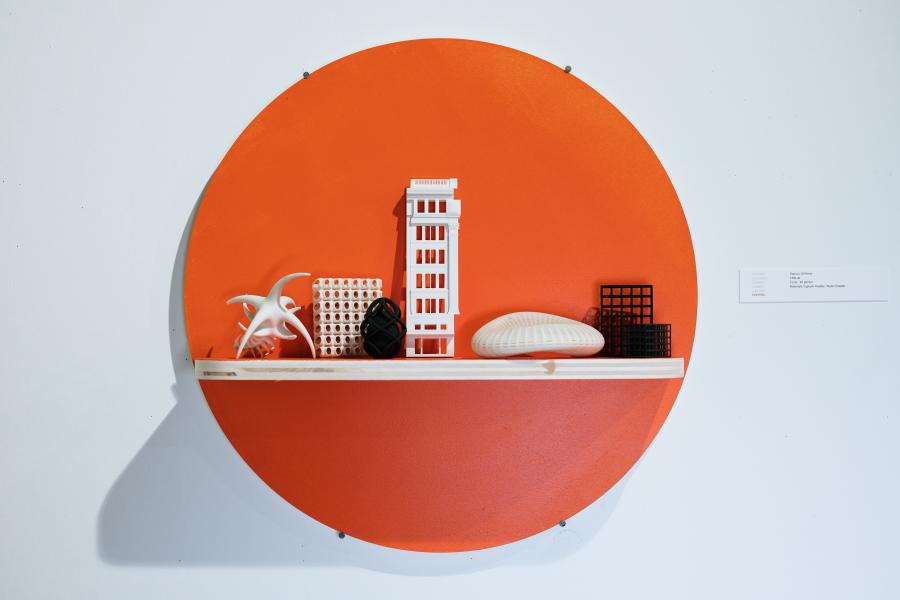
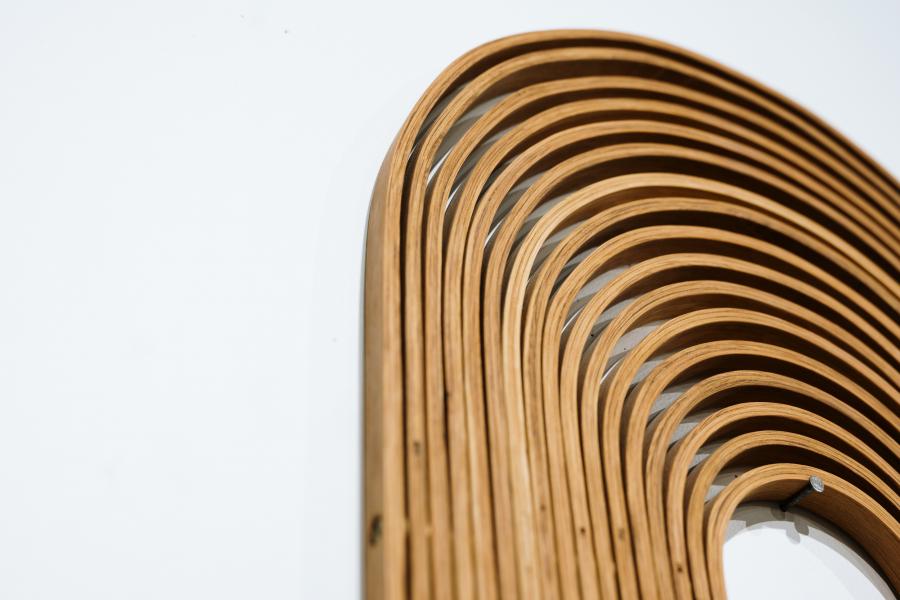
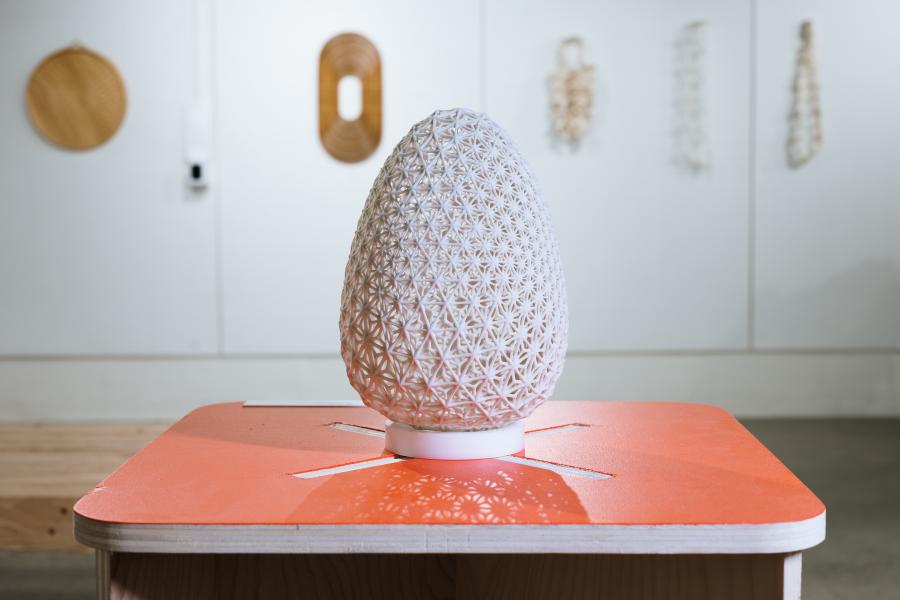
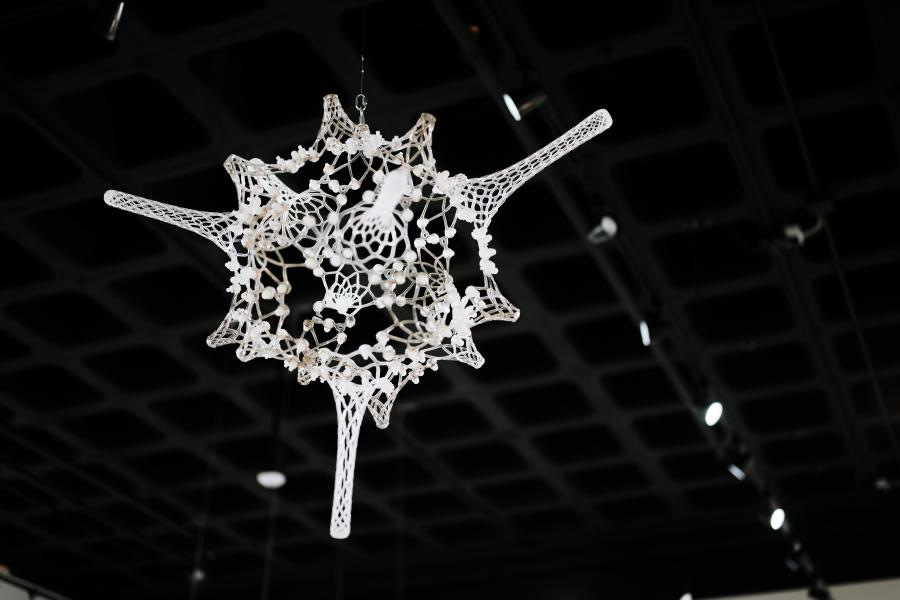
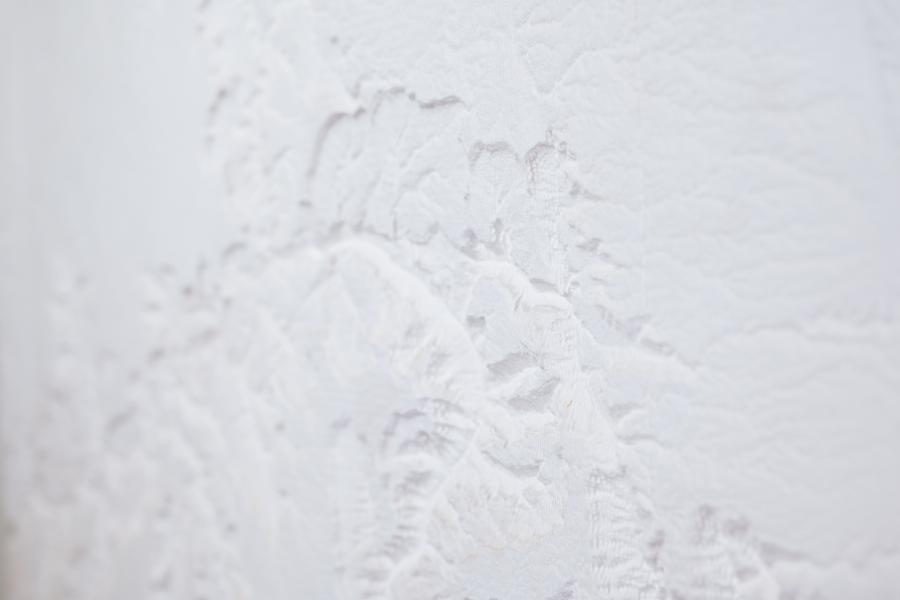
Cani⊥lever Bench
From acetylated to reclaimed. From managed to manufactured. Forests, as a series of living beings, hold capacity and cultivate sustainable bodies. The Canitlever project was a collaborative effort on the part of students, staff and local industry to visually and structurally express the fibrous nature of reclaimed wood. As part of a means to reach the 2019-2023 goals and commitments, as outlined in the University of Manitoba’s Sustainability Strategy. The story of CANI┴LEVER began in 2016, with a partnership between the Faculty of Architecture’s FABLab and Upper Canada Forest Products (UCFP). The FABLab assembled a team of students and staff, tasked by UCFP with the following challenge: demonstrate the design potential of Accoya wood. The trick is, “Accoya” as a species does not actually exist. It is manufactured from fast-growing pine trees and treated with acetic acid, greatly improving the wood’s density and durability. The resulting Accoya bench was dubbed CANI┴LEVER, a structural enigma at first glance, revealed to be a feat of careful craftsmanship upon further inspection.
The next year brought an onslaught of construction to the UofM’s Fort Garry campus. Infrastructure renewal projects caused vast tree removal, with Wood Anchor and WPG Timber Co. working to salvage as many as possible for milling and reuse. The mass availability of reclaimed wood was the first factor to align for the next chapter in CANI┴LEVER’s story. In 2019, the second factor aligned, as construction began on the refurbishment of the Allen Building walkway. The redesign of this outdoor corridor was taken on by Little Bluestem Landscape Architecture. In this new public space, a ‘reclaimed’ version of CANI┴LEVER was specified, to give a second life to the trees that had come down earlier that spring. To fulfill these new design requirements, the FABLab connected with experts beyond their original team. Construction industry partners offered guidance for the addition of a concrete base and a retooled seat. A graduate student from the Faculty of Engineering performed a virtual stress test using Finite Element Analysis. An architecture co-op student assisted in the modeling and fabrication of the benches. At each stage of design, collaboration was key. As a result of the design challenge issued by UCFP almost six years ago, the FABLab has built interdisciplinary connections, contributed to campus sustainability initiatives, and curated new skills and knowledge related to methods of fabrication.
Project Lead |
Jason Hare – University of Manitoba
Project Designers |
Kellen Deighton, Jane Hilder, Jon Watts, Kim Wiese, Colby Cook
Project Collaborators |
Barkman Concrete \ CAST \ Little Bluestem \ UofM OOS \ UofM Physical Plant \ Wood Anchor
Project Contributors |
Jasper Arthur \ Seema Goel \ Benita Kliewer \ Chris Pancoe
Fabricator |
FAUM FABLab
Project Lead |
Jason Hare – University of Manitoba
Project Designers |
Kellen Deighton, Jane Hilder, Jon Watts, Kim Wiese, Colby Cook
Project Collaborators |
Barkman Concrete \ CAST \ Little Bluestem \ UofM OOS \ UofM Physical Plant \ Wood Anchor
Project Contributors |
Jasper Arthur \ Seema Goel \ Benita Kliewer \ Chris Pancoe
Fabricator |
FAUM FABLab
Project Lead |
Jason Hare – University of Manitoba
Project Designers |
Kellen Deighton, Jane Hilder, Jon Watts, Kim Wiese, Colby Cook
Project Collaborators |
Barkman Concrete \ CAST \ Little Bluestem \ UofM OOS \ UofM Physical Plant \ Wood Anchor
Project Contributors |
Jasper Arthur \ Seema Goel \ Benita Kliewer \ Chris Pancoe
Fabricator |
FAUM FABLab
Project Lead |
Jason Hare – University of Manitoba
Project Designers |
Kellen Deighton, Jane Hilder, Jon Watts, Kim Wiese, Colby Cook
Project Collaborators |
Barkman Concrete \ CAST \ Little Bluestem \ UofM OOS \ UofM Physical Plant \ Wood Anchor
Project Contributors |
Jasper Arthur \ Seema Goel \ Benita Kliewer \ Chris Pancoe
Fabricator |
FAUM FABLab
Project Lead |
Jason Hare – University of Manitoba
Project Designers |
Kellen Deighton, Jane Hilder, Jon Watts, Kim Wiese, Colby Cook
Project Collaborators |
Barkman Concrete \ CAST \ Little Bluestem \ UofM OOS \ UofM Physical Plant \ Wood Anchor
Project Contributors |
Jasper Arthur \ Seema Goel \ Benita Kliewer \ Chris Pancoe
Fabricator |
FAUM FABLab
Project Lead |
Jason Hare – University of Manitoba
Project Designers |
Kellen Deighton, Jane Hilder, Jon Watts, Kim Wiese, Colby Cook
Project Collaborators |
Barkman Concrete \ CAST \ Little Bluestem \ UofM OOS \ UofM Physical Plant \ Wood Anchor
Project Contributors |
Jasper Arthur \ Seema Goel \ Benita Kliewer \ Chris Pancoe
Fabricator |
FAUM FABLab
Project Lead |
Jason Hare – University of Manitoba
Project Designers |
Kellen Deighton, Jane Hilder, Jon Watts, Kim Wiese, Colby Cook
Project Collaborators |
Barkman Concrete \ CAST \ Little Bluestem \ UofM OOS \ UofM Physical Plant \ Wood Anchor
Project Contributors |
Jasper Arthur \ Seema Goel \ Benita Kliewer \ Chris Pancoe
Fabricator |
FAUM FABLab
Project Lead |
Jason Hare – University of Manitoba
Project Designers |
Kellen Deighton, Jane Hilder, Jon Watts, Kim Wiese, Colby Cook
Project Collaborators |
Barkman Concrete \ CAST \ Little Bluestem \ UofM OOS \ UofM Physical Plant \ Wood Anchor
Project Contributors |
Jasper Arthur \ Seema Goel \ Benita Kliewer \ Chris Pancoe
Fabricator |
FAUM FABLab
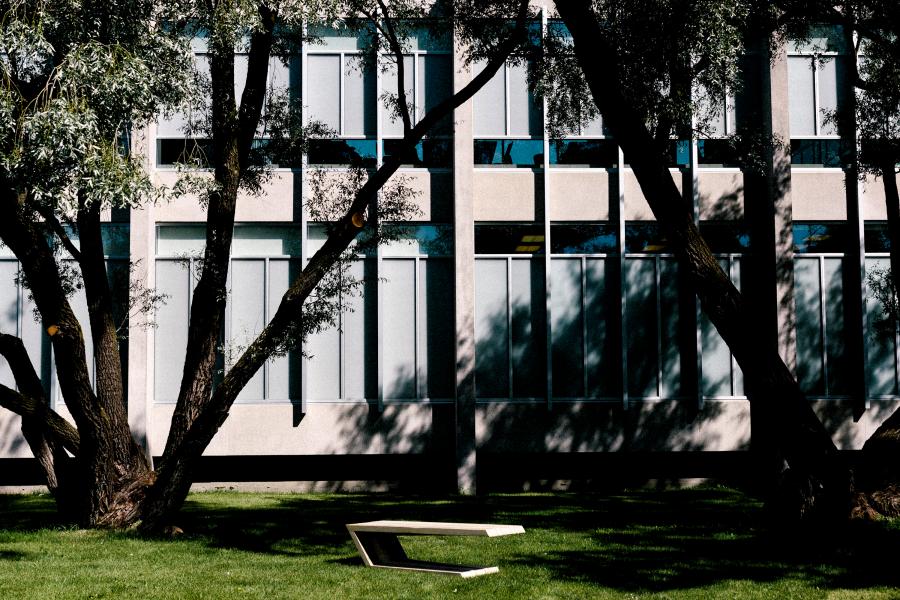
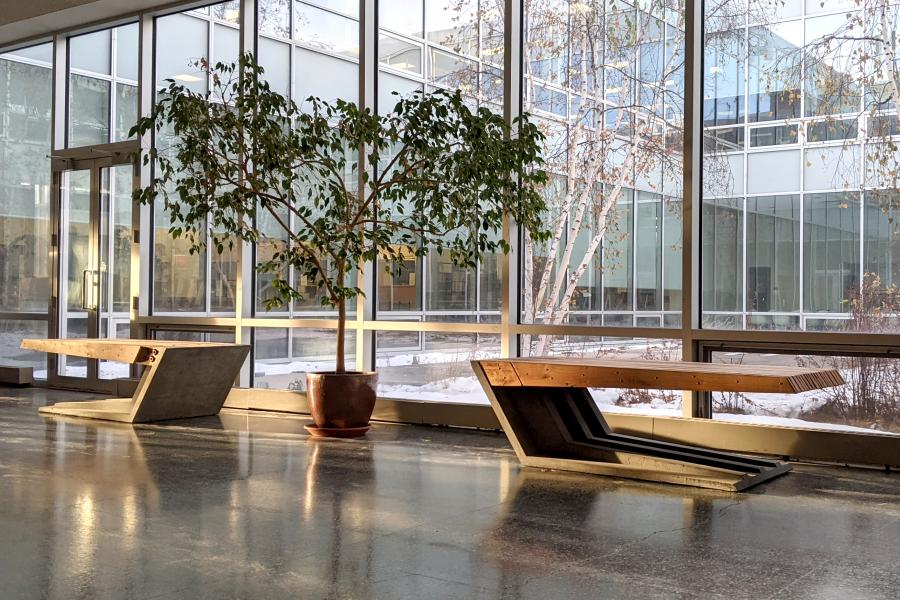
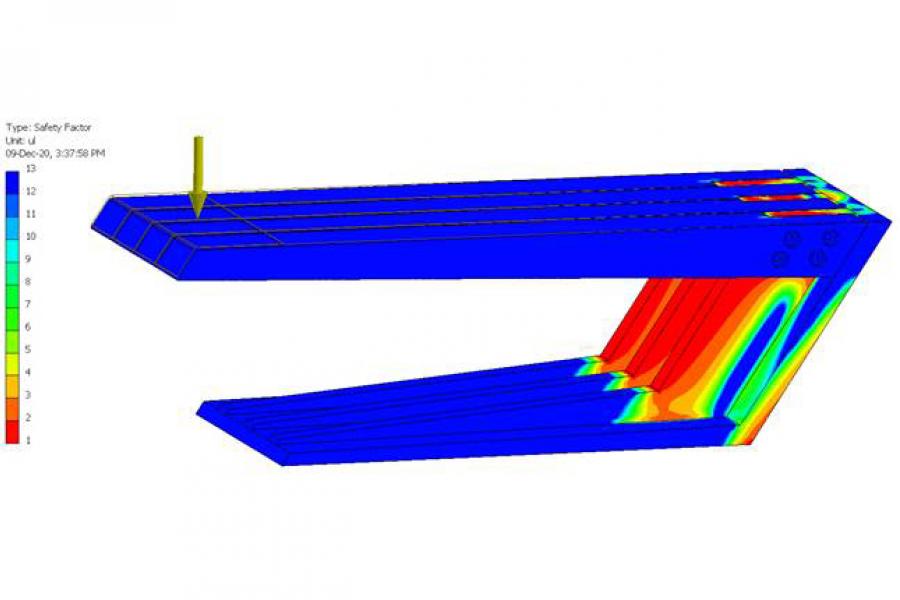
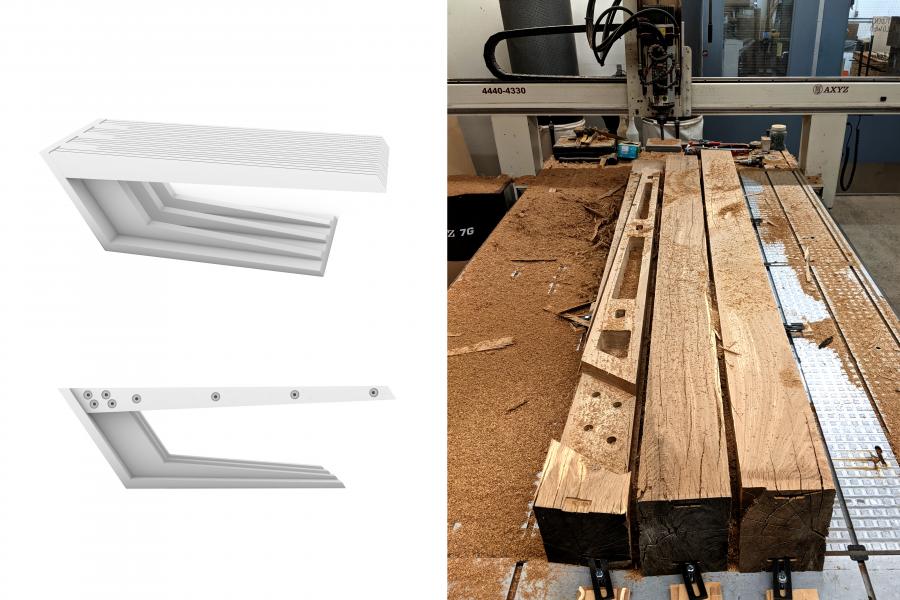
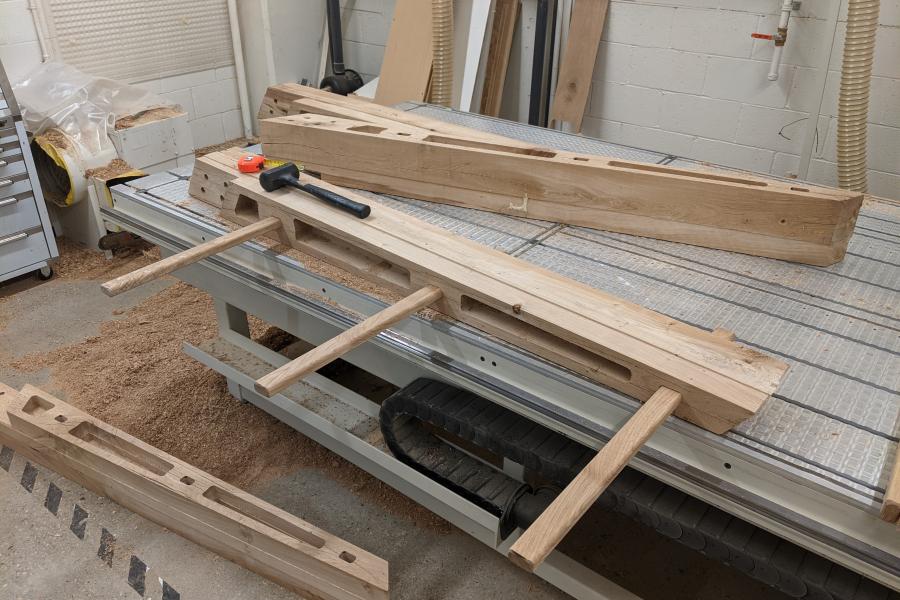
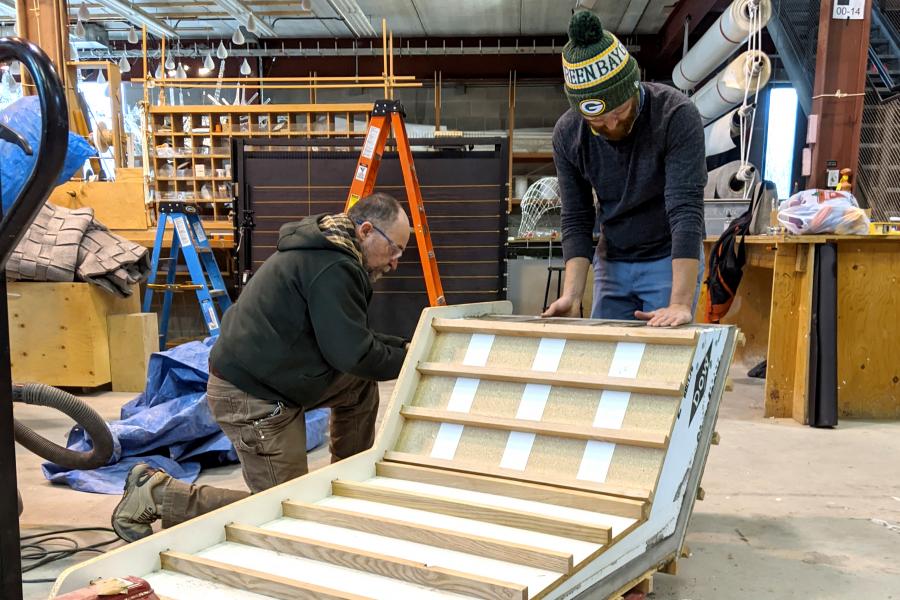
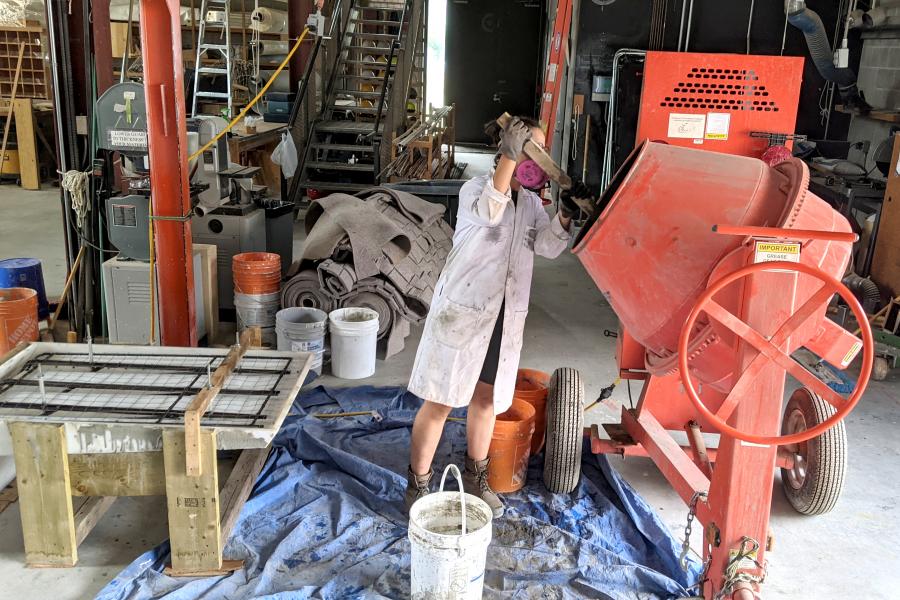
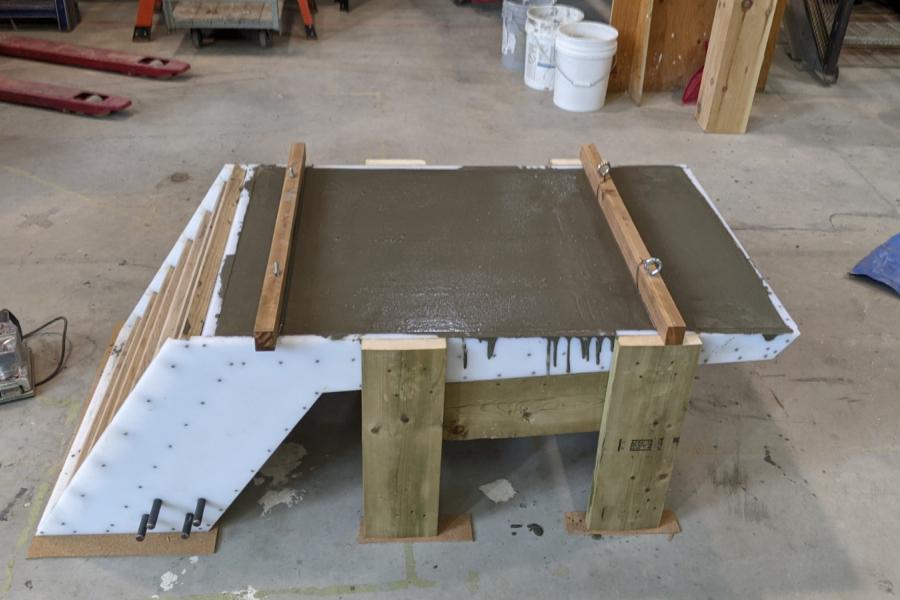
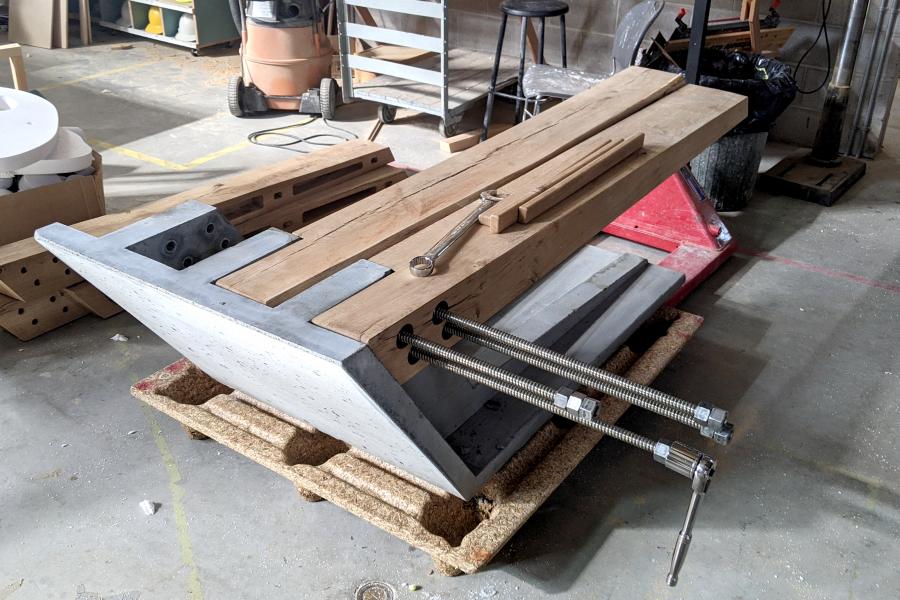

Fabrigami
Fabric and ice shells, first pioneered by Heinz Isler (Chilton [2]), are lightweight structural systems that allow for inexpensive and reversible construction of free-standing stiffened shell structures. They are of interest for exploring new structural forms and construction methods and are analogs for shells built with more permanent materials. Fabrigami was a project that sought to exploit both the methods of origami forming, as well as the structural performance of origami geometries to create a folded fabric ice shell. The project introduced a new formal and structural typology for fabric-based shell structures, taking inspiration from origami and folded plate structures but also utilizing the curved geometry of stretched fabric for added structural stiffness. This was achieved through the use of flexible and pliable construction materials (fabric and water) that was then rigidified (frozen) to arrive at the resulting form. The project resulted in a free-standing fabric formed ice shell (0.6 - 3 cm thick) that supported 2,195 kg. of dead load, spanning 11.5m x 6.6m x 3.2m.
Project Partners |
Dr. Caitlin Mueller, the Digital Structures Lab - MIT
Dr. Lars de Laet, AE Lab - Vrije University, Brussels
Jason Hare - University of Manitoba
Lancelot Coar - University of Manitoba
Kim Wiese - University of Manitoba
Steven Oberlin - University of Manitoba
Project Partners |
Dr. Caitlin Mueller, the Digital Structures Lab - MIT
Dr. Lars de Laet, AE Lab - Vrije University, Brussels
Jason Hare - University of Manitoba
Lancelot Coar - University of Manitoba
Kim Wiese - University of Manitoba
Steven Oberlin - University of Manitoba
Project Partners |
Dr. Caitlin Mueller, the Digital Structures Lab - MIT
Dr. Lars de Laet, AE Lab - Vrije University, Brussels
Jason Hare - University of Manitoba
Lancelot Coar - University of Manitoba
Kim Wiese - University of Manitoba
Steven Oberlin - University of Manitoba
Project Partners |
Dr. Caitlin Mueller, the Digital Structures Lab - MIT
Dr. Lars de Laet, AE Lab - Vrije University, Brussels
Jason Hare - University of Manitoba
Lancelot Coar - University of Manitoba
Kim Wiese - University of Manitoba
Steven Oberlin - University of Manitoba
Project Partners |
Dr. Caitlin Mueller, the Digital Structures Lab - MIT
Dr. Lars de Laet, AE Lab - Vrije University, Brussels
Jason Hare - University of Manitoba
Lancelot Coar - University of Manitoba
Kim Wiese - University of Manitoba
Steven Oberlin - University of Manitoba
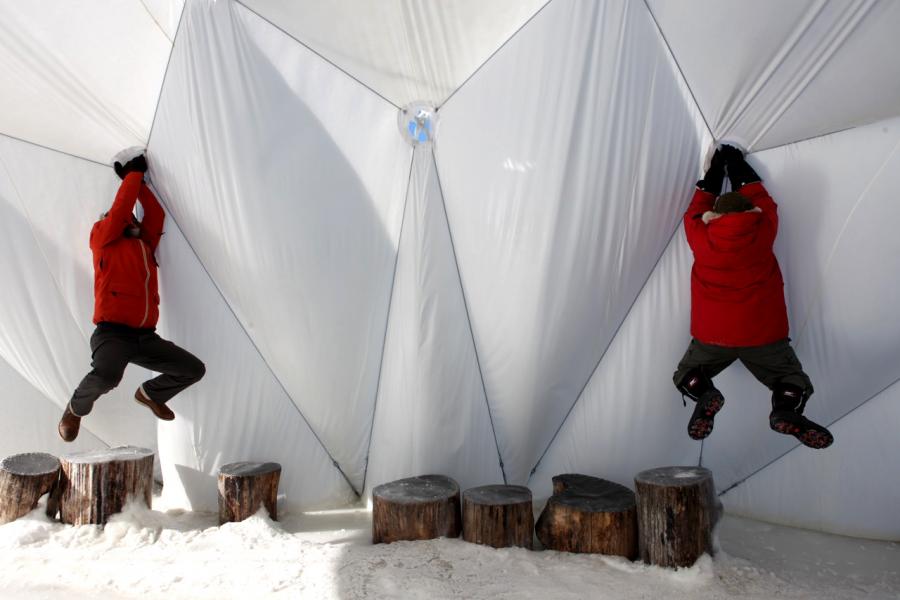
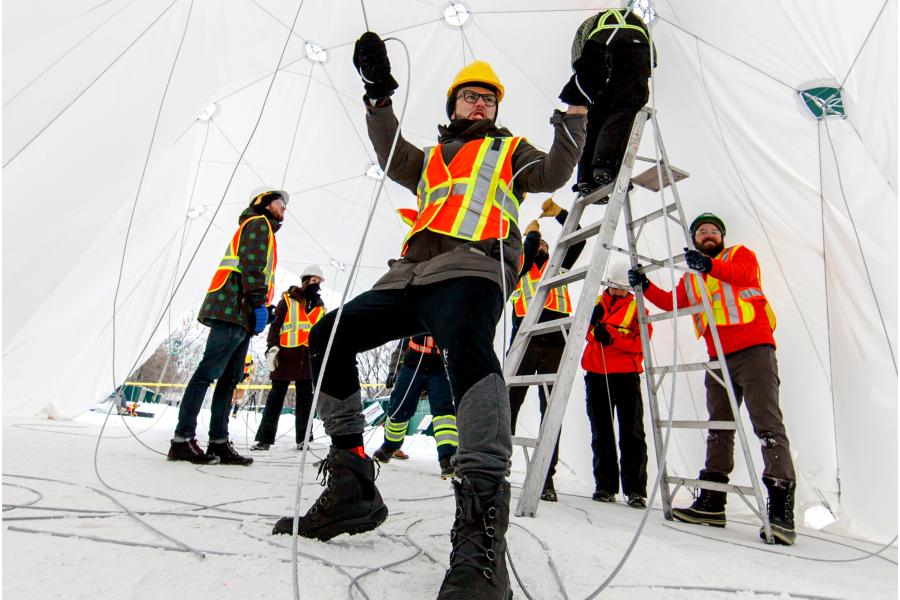
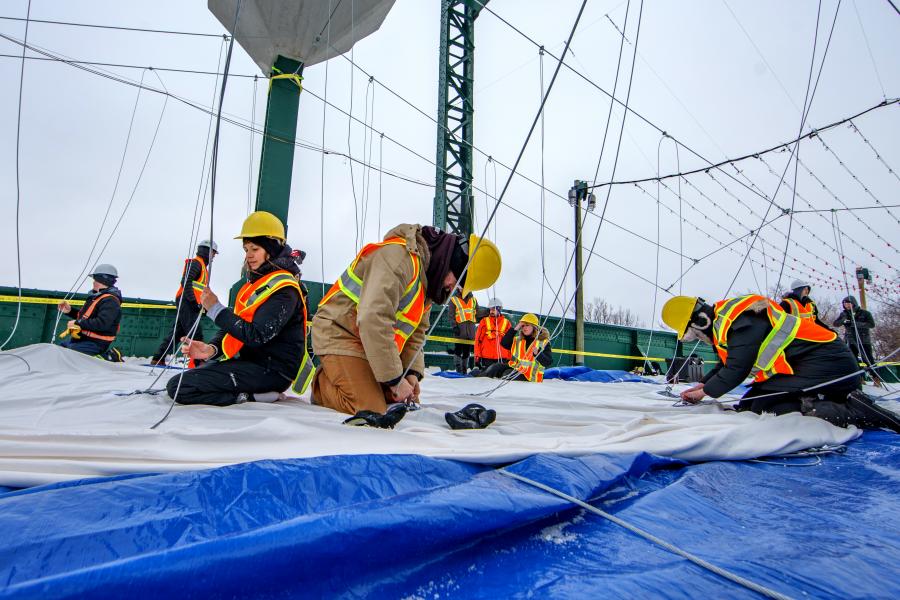
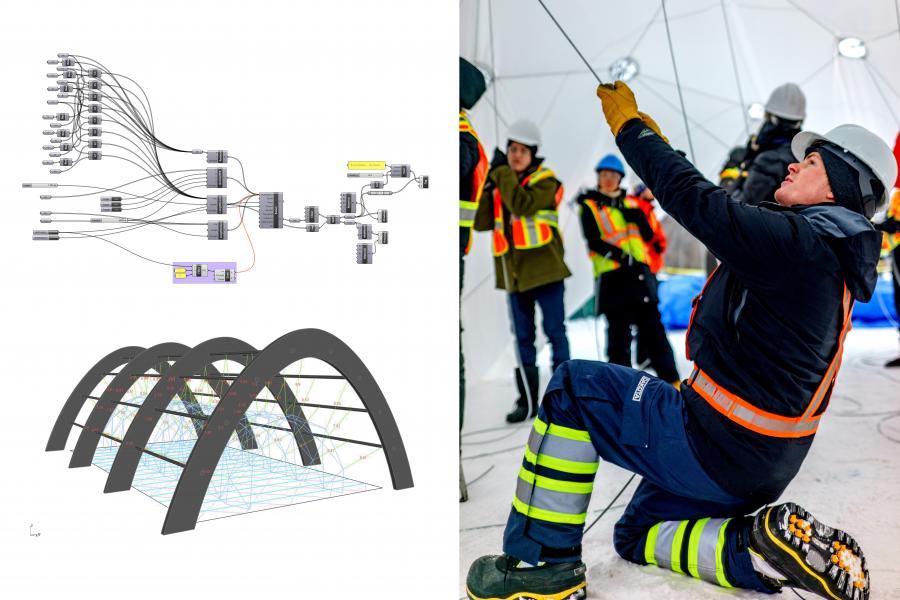
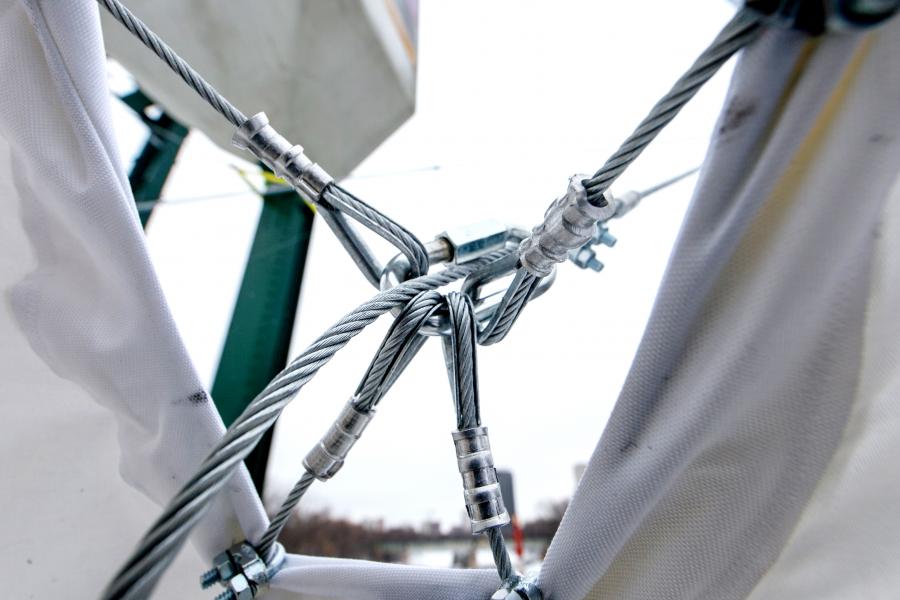
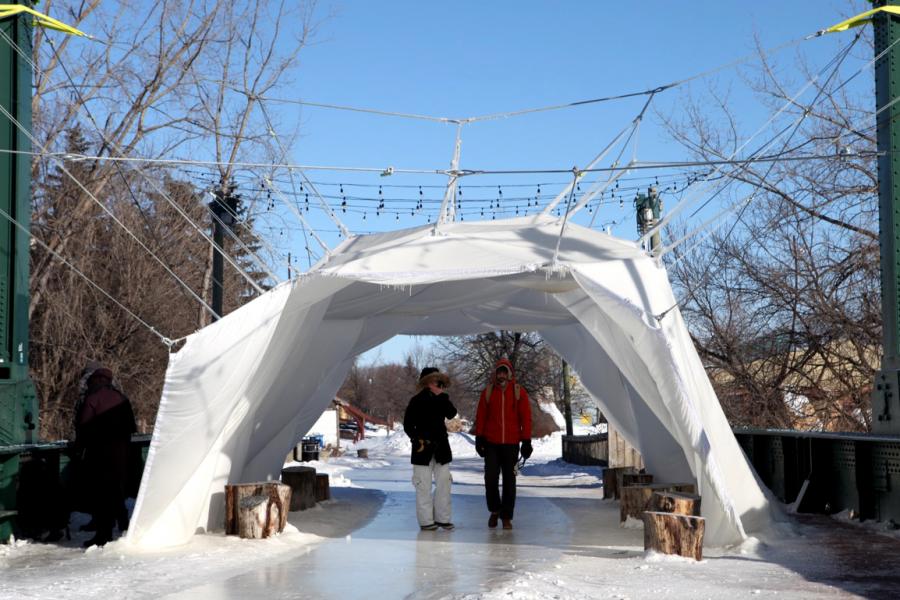
Campus Model
The University of Manitoba was founded in 1877. It was digitized in 2021. The FABLab team spent 3 years creating a detailed model of the University of Manitoba Fort Garry Campus. A photo catalog of buildings on campus was created by the FABLab team to aid in modelling. Measurements from Google Earth were essential in the model making process. Every window, wall, and door were individually modelled to match the layout of campus. The model consists of over 80 fully 3D modelled buildings on campus (everything east of University Crescent to the river). The building models were crafted in Rhinoceros 3D using a multitude of drawing sets from over the years. Some of the buildings did not have drawings available, and most of the ones that did were old and hand drawn. This required a lot of tracing and redrafting in the model making process. Now that the models are made, a drawing set could easily be output from the 3D models. Each building is a watertight polysurface modelled so it can easily be scaled and 3D printed.
The campus model was funded by the Campus planning office along with volunteered time by the FABLab team. For access to the model, please contact the FABLab.
Project Collaborators |
FABLab
Campus Planning Office
Jon Watts
Project Collaborators |
FABLab
Campus Planning Office
Jon Watts
Project Collaborators |
FABLab
Campus Planning Office
Jon Watts
Project Collaborators |
FABLab
Campus Planning Office
Jon Watts
Project Collaborators |
FABLab
Campus Planning Office
Jon Watts
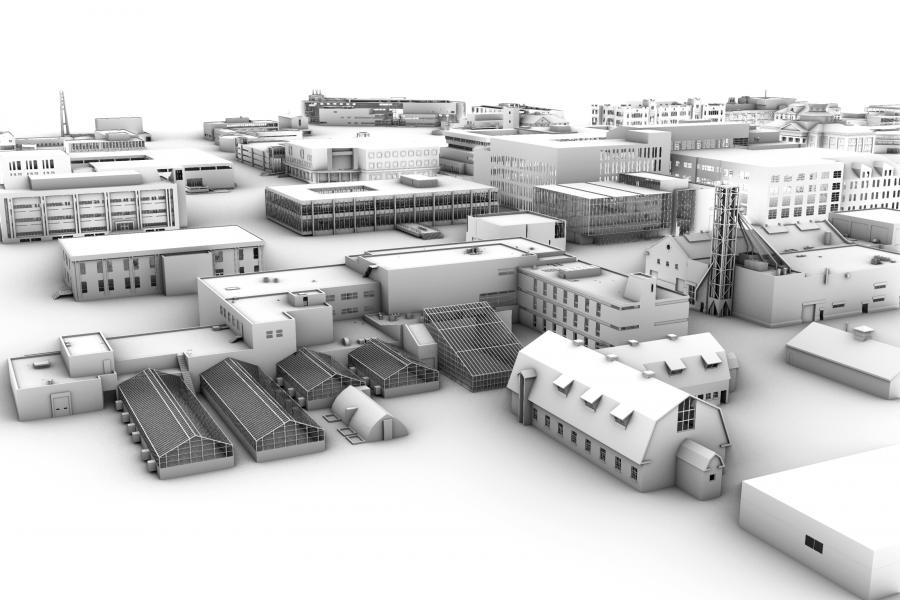
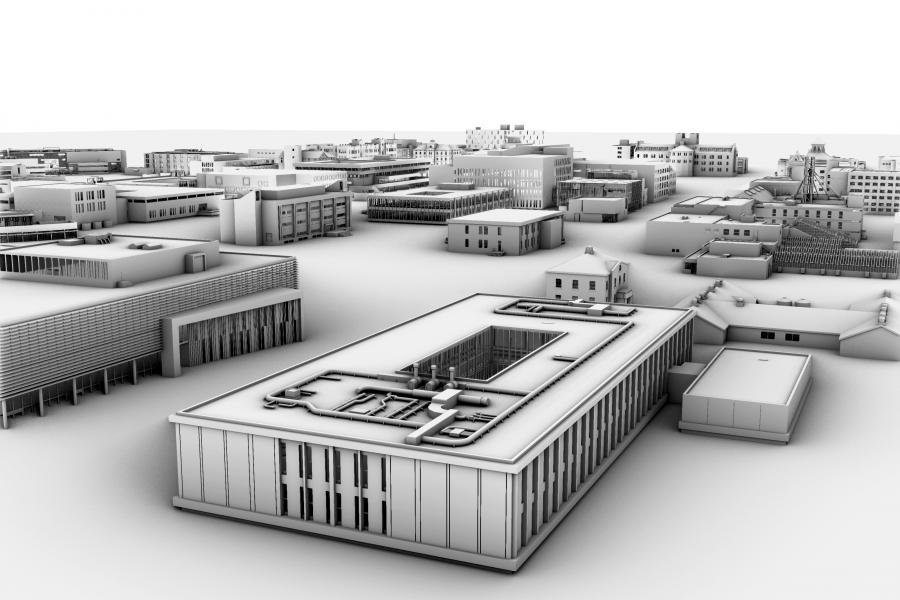
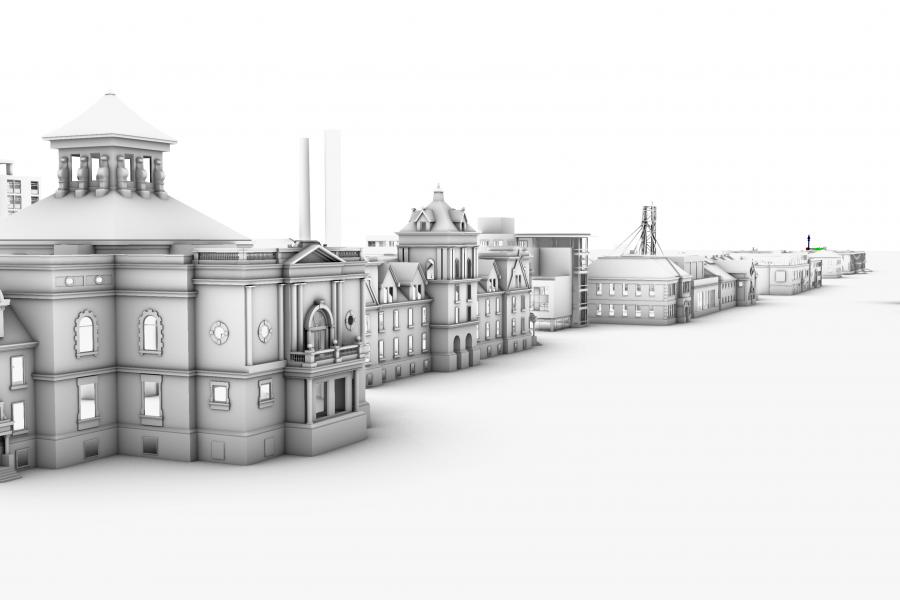
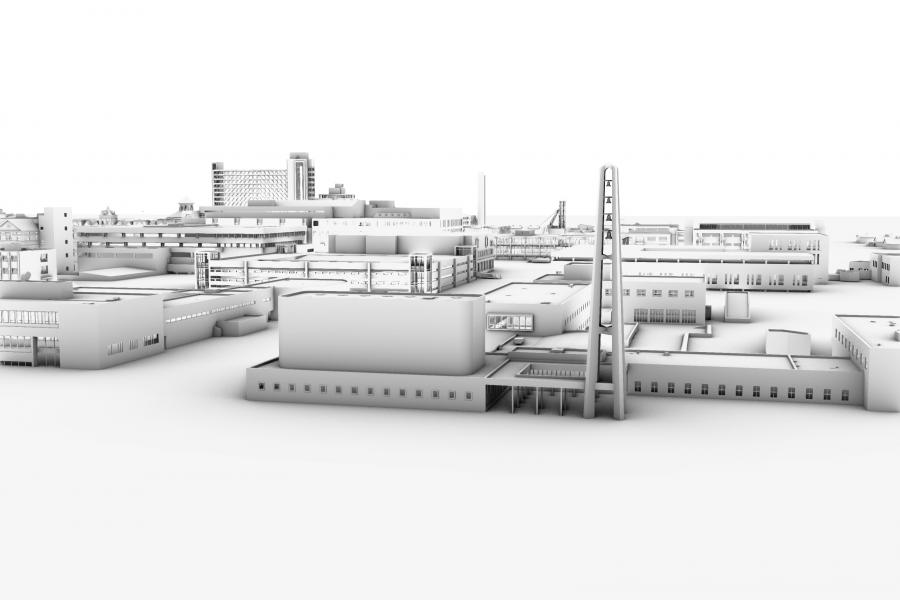
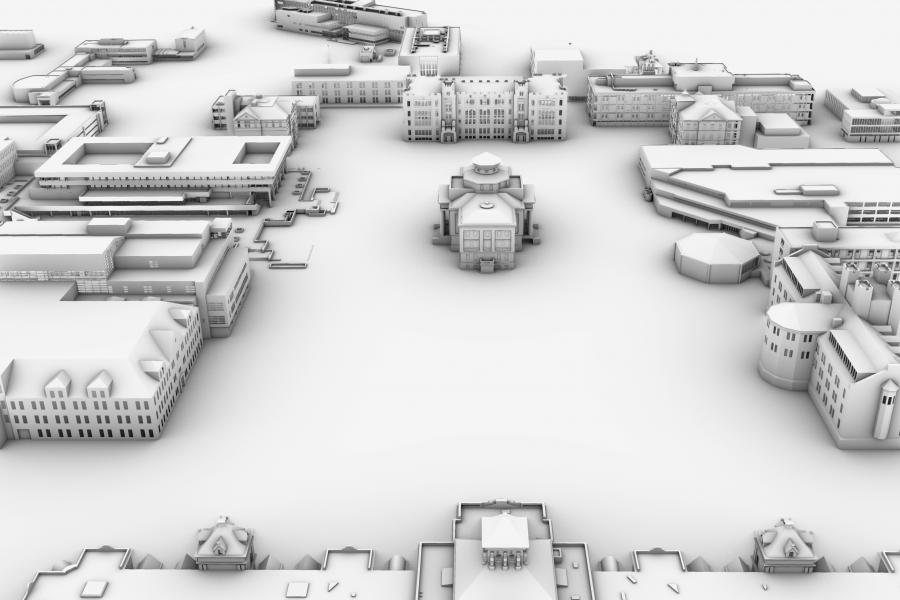
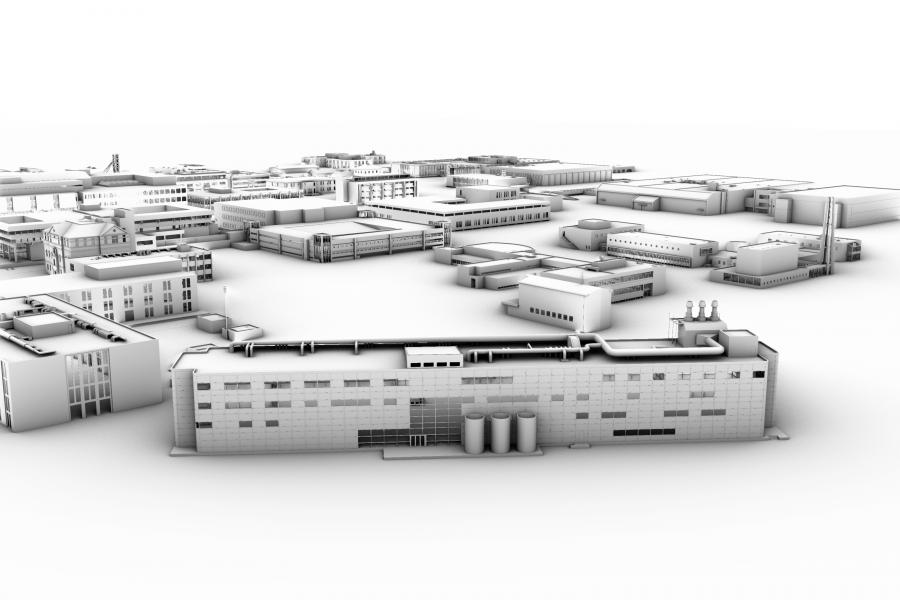
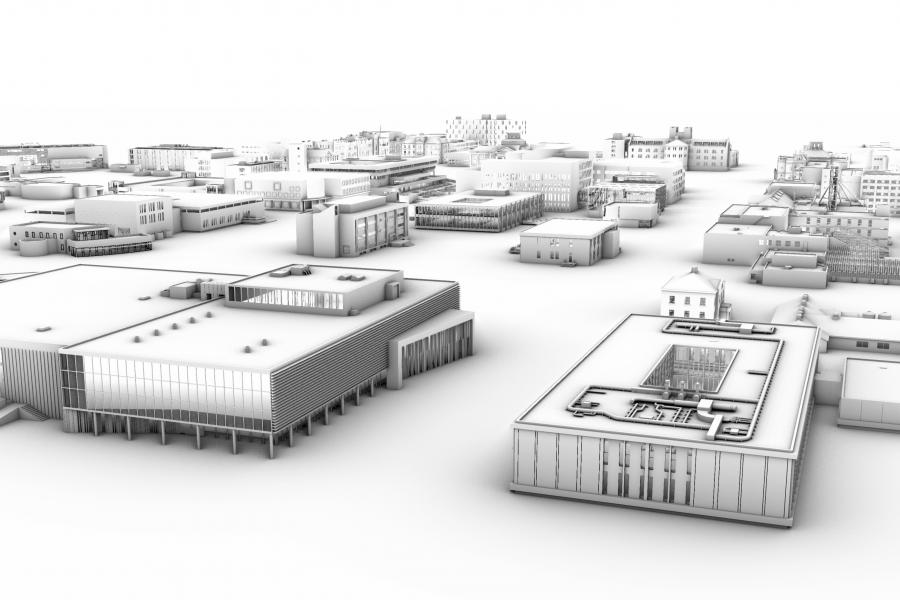
Bee House Lab
Bees are instrumental in the pollination of various plant systems. Three quarters of the world’s flowering plants and over one third of the world’s food crops depend on pollinators. Pollinator communities, including solitary nesting bees, are under pressure from habitat loss occurred by urban development and a patchwork of biological diverse landscapes. Pollinators play a critical role in the health of ecosystems. Small changes to human practices and mindfulness about habitat preservation can have a significant positive impact on pollinators.
Digital fabrication enables designers to engage the living research on bee habitat at the crossroads of environment science, engineering, computation, material science, and biology. Through digital design-modelling and prototype-fabrication, Digital Design and Fabrication can contribute to the living research focused on the space-form-habitat relationship at its micro scale.
Bee House Lab was an international design competition hosted by the University of Manitoba and open to students and designers in the field of Environmental Design, Architecture, Landscape Architecture, Industrial Design, and other related fields. The competition called for a design of a bee house prototype that could be fabricated and deployed for field testing. More than 100 houses were field-tested to study their space-form-habitat performance.
The competition was hosted by the University’s Office of Sustainability, and supported by the FABLab at the Faculty of Architecture, the Department of Entomology and Parks Canada Campus Club at the University of Manitoba. STUFF (Studio for Transformative Urban Forms and Fields) served as the design competition coordinator.
Project Partners |
UofM Office of Sustainability, UofM FABLab, UofM Department of Entomology, Parks Campus Club, STUFF.
Competition Winners |
Owen Nichols, Anca Matiyaku, Chad Connery, Meaghan Krahn, Brandon Bergem, Derek Smart, Michael Mazurkiewicz, Evan Taylor, Matt Hagen
Project Partners |
UofM Office of Sustainability, UofM FABLab, UofM Department of Entomology, Parks Campus Club, STUFF.
Competition Winners |
Owen Nichols, Anca Matiyaku, Chad Connery, Meaghan Krahn, Brandon Bergem, Derek Smart, Michael Mazurkiewicz, Evan Taylor, Matt Hagen
Project Partners |
UofM Office of Sustainability, UofM FABLab, UofM Department of Entomology, Parks Campus Club, STUFF.
Competition Winners |
Owen Nichols, Anca Matiyaku, Chad Connery, Meaghan Krahn, Brandon Bergem, Derek Smart, Michael Mazurkiewicz, Evan Taylor, Matt Hagen
Project Partners |
UofM Office of Sustainability, UofM FABLab, UofM Department of Entomology, Parks Campus Club, STUFF.
Competition Winners |
Owen Nichols, Anca Matiyaku, Chad Connery, Meaghan Krahn, Brandon Bergem, Derek Smart, Michael Mazurkiewicz, Evan Taylor, Matt Hagen
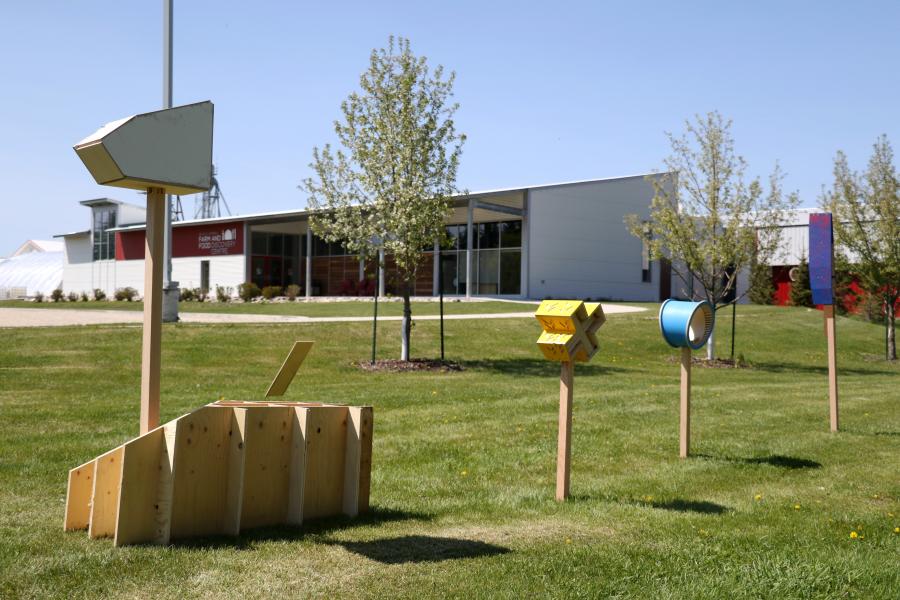
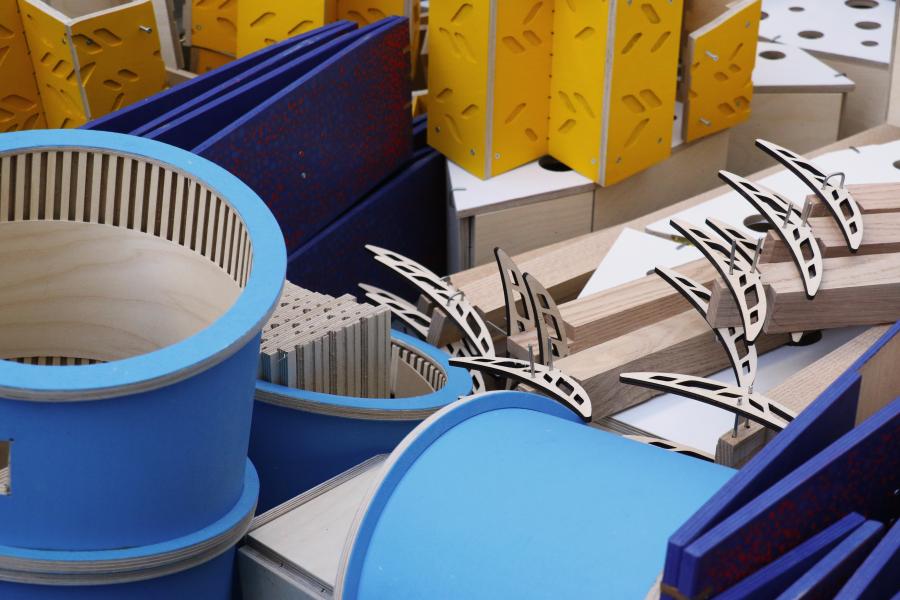
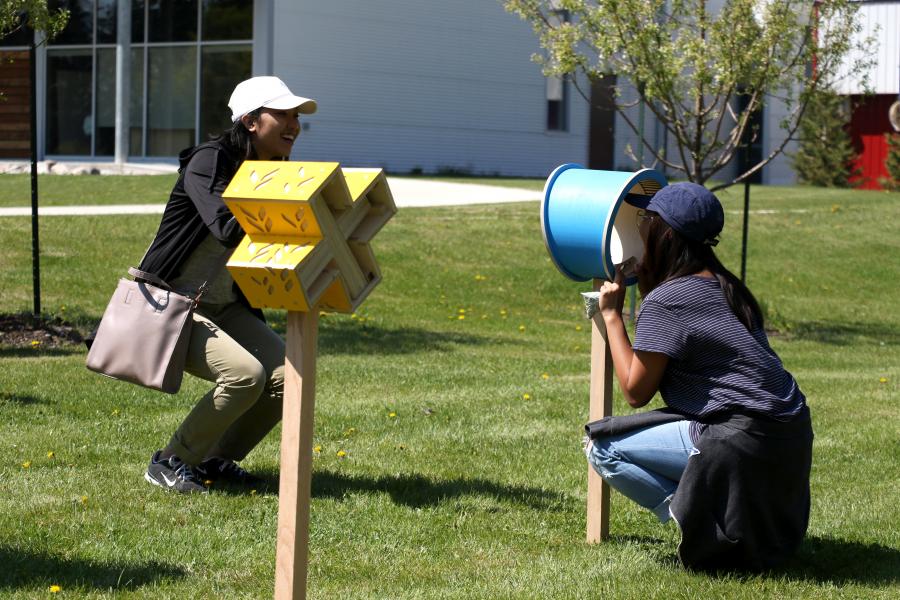
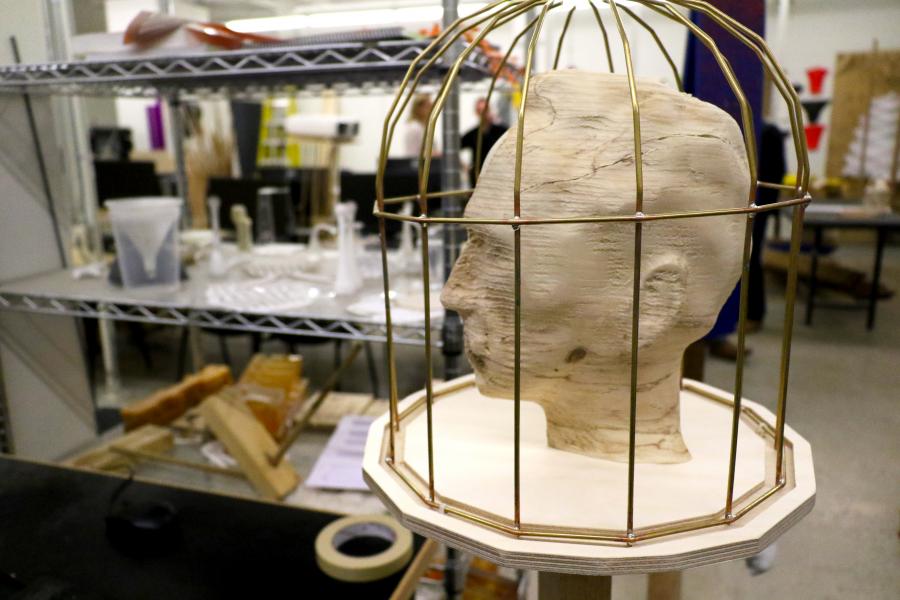
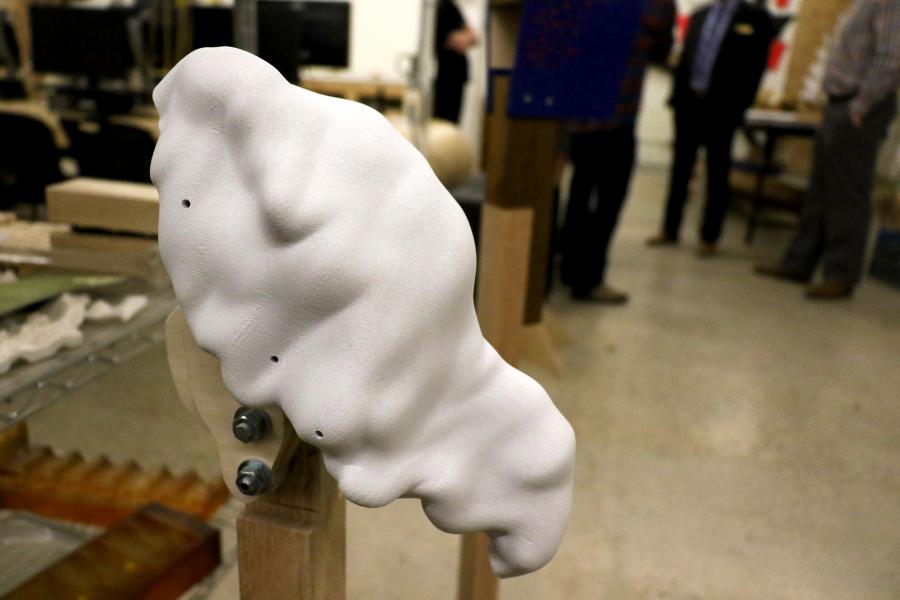
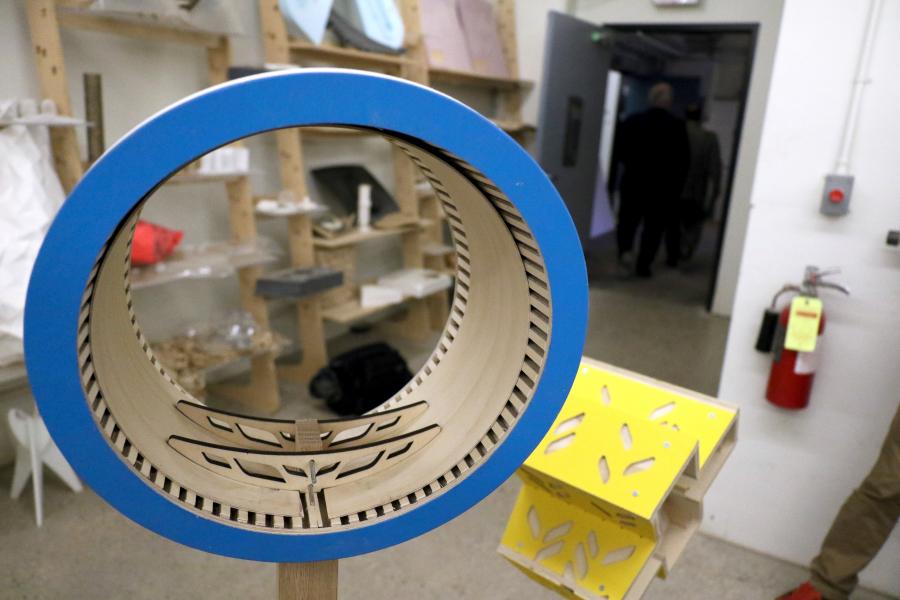
Manitoba Museum Groteques
The Winnipeg Tribune Building came crashing down in 1983. The roof that had once been dotted with Grotesques now lay flat on the ground. Each of these Grotesques is modelled after a character, and tells its own story. After the demolition of this 6 storey building, the Grotesques ended up scattered across the country. Eventually a few of them made their way to The Manitoba Museum. With the intention of recreating the old Winnipeg Tribune Building, The Manitoba Museum got in contact with the FABLab. They set out to replicate these Grotesques for integration into an exhibit.
Photo credit: Manitoba Museaum
The workflow went something like this: The models were 3D scanned using a white light scanner. The models were then patched up digitally using Rhinoceros 3D. After being patched up the models were re-sculpted using zBrush to add all the details that were left out from the 3D scan. Additional elements were modelled in Rhinoceros 3D and unioned to the models. The meshes were then reconstructed in Meshlabs and then 3D printed out of PLA (plant based plastic) at Objex. The prints were then painted up to look like stone, and installed at the Manitoba Museum. These are by far the largest 3D prints the FABLab has ever worked with to date.
Photo credit: Manitoba Museaum
Project Collaborators |
Jon Watts
Cindy Colford
Roland Sawatzky
Photo credit: Manitoba Museaum
Project Collaborators |
Jon Watts
Cindy Colford
Roland Sawatzky
Photo credit: Manitoba Museaum
Project Collaborators |
Jon Watts
Cindy Colford
Roland Sawatzky
Project Collaborators |
Jon Watts
Cindy Colford
Roland Sawatzky
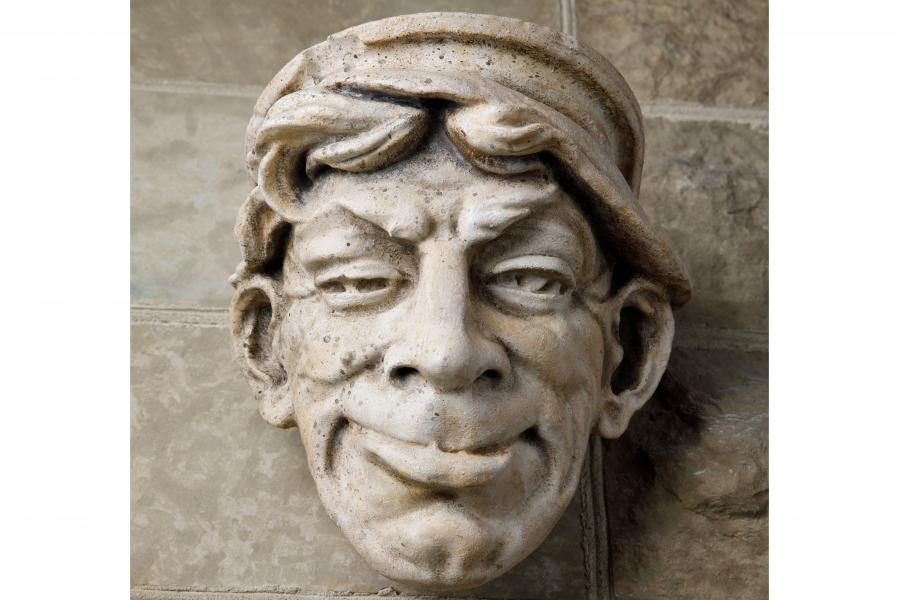
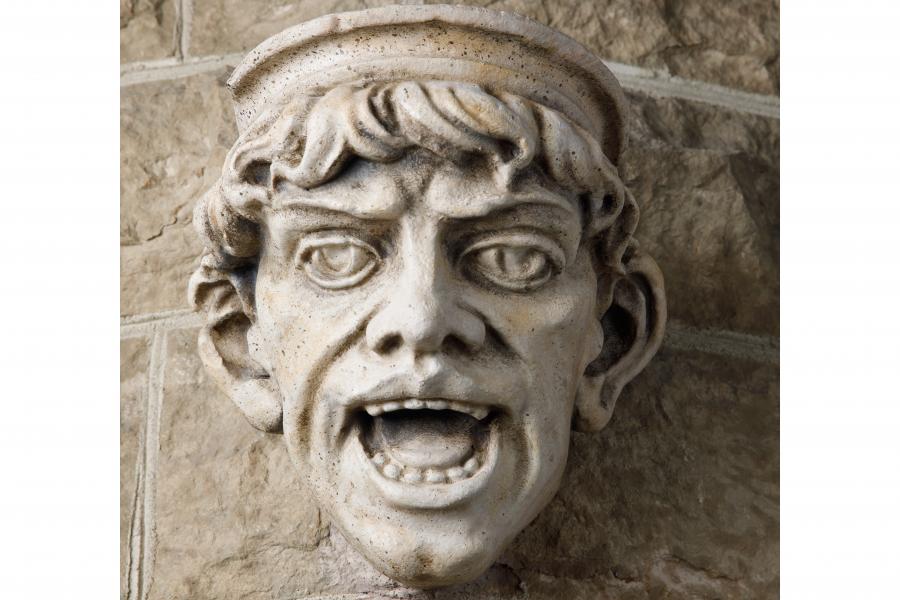
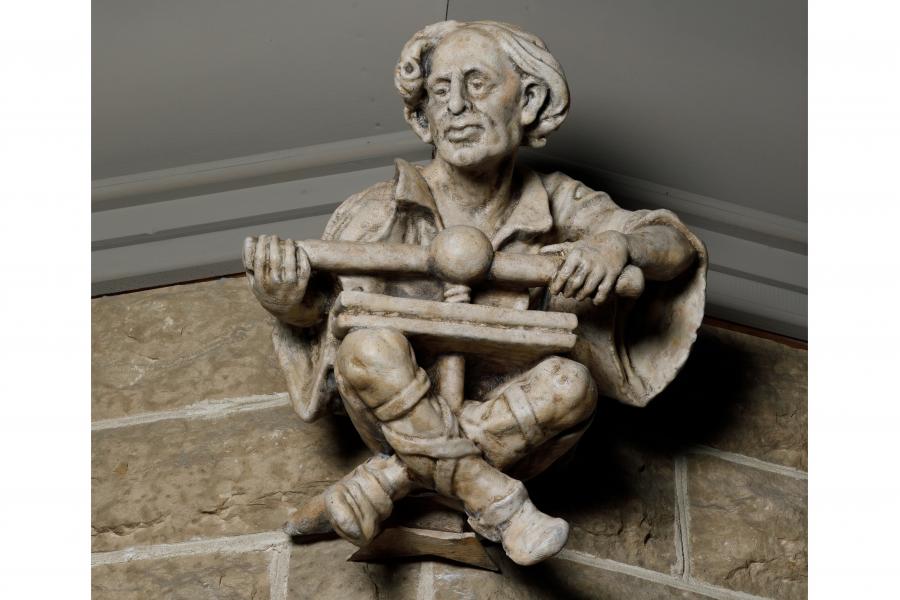
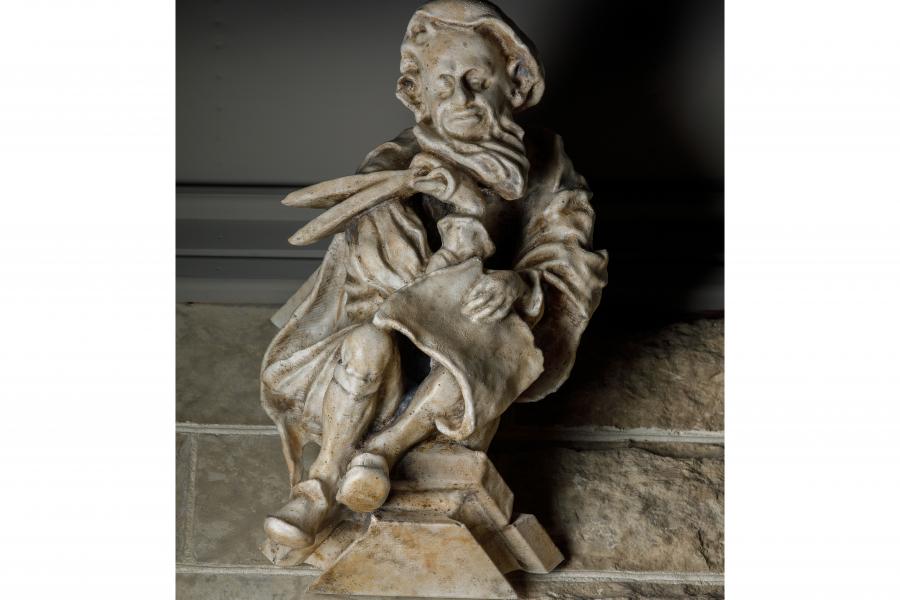
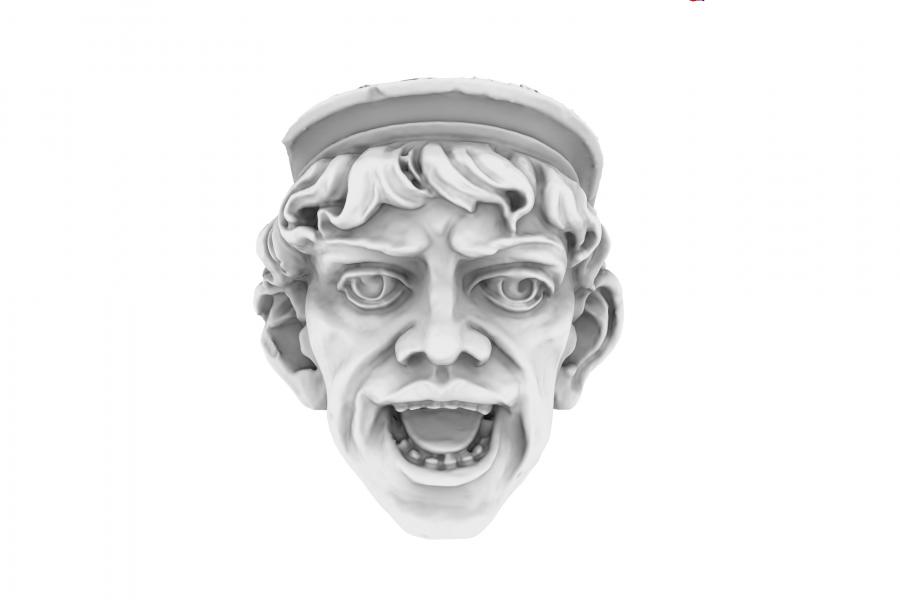
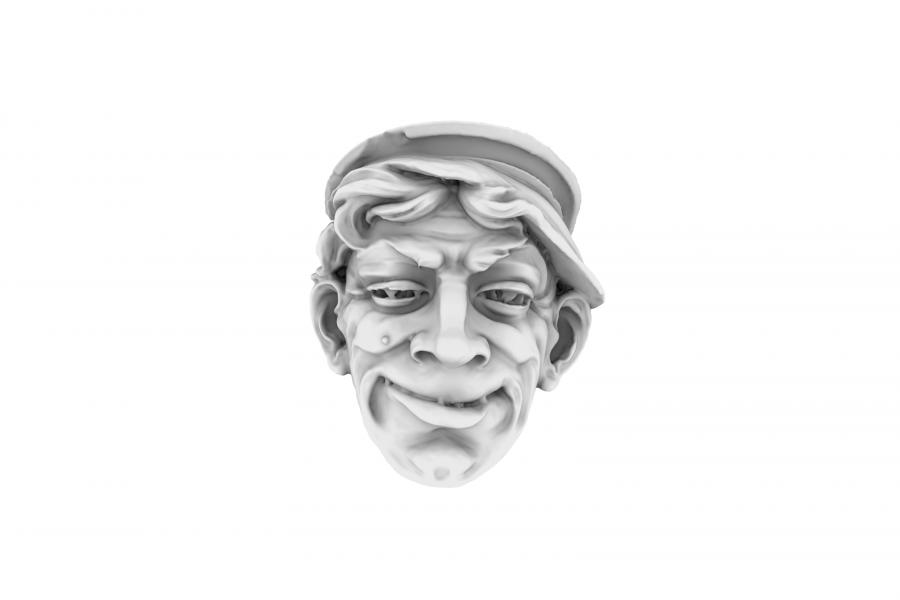
Bee Cuddler
In collaboration with Winnipeg’s Beeproject Apiaries. The bee cuddler was envisioned as a means to directly view the inner workings of an active bee colony. As well as a teaching tool towards understanding how our pollinating ‘producers’ support a rich ecology of diverse beings.
As pollinator populations, including that of the honeybee have been critically threatened around the world. This project looked to establish an experimental hive, based on the standardized dimensions of the Lanstroth frame. Within the workshop portion of this project, a series of experimental hives were developed with academic’s, students, technicians and producers alike. Ultimately landing on the notion that seeing inside the walls of the Lanstroth hive would present the viewer with new insight and value to the role these critical creatures play. The installation was in place for the summer of 2017, with recordings taken on the weekly health of the hive. Ultimately the form proved valuable as a means of temporarily viewing bees but was not suitable as a permanent hive over an entire season.
Project Lead |
Lindsay and Chris Kirouac - Beeproject Apiaries
Jason Hare – University of Manitoba
Project Collaborators |
Kim Wiese, Jon Watts, Juilana Kusyk, Anetta Los, Rachelle Kirouac, Benjamin Bosiak, Anna Thurmayr, Dietmar Straub
Project Lead |
Lindsay and Chris Kirouac - Beeproject Apiaries
Jason Hare – University of Manitoba
Project Collaborators |
Kim Wiese, Jon Watts, Juilana Kusyk, Anetta Los, Rachelle Kirouac, Benjamin Bosiak, Anna Thurmayr, Dietmar Straub
Project Lead |
Lindsay and Chris Kirouac - Beeproject Apiaries
Jason Hare – University of Manitoba
Project Collaborators |
Kim Wiese, Jon Watts, Juilana Kusyk, Anetta Los, Rachelle Kirouac, Benjamin Bosiak, Anna Thurmayr, Dietmar Straub
Project Lead |
Lindsay and Chris Kirouac - Beeproject Apiaries
Jason Hare – University of Manitoba
Project Collaborators |
Kim Wiese, Jon Watts, Juilana Kusyk, Anetta Los, Rachelle Kirouac, Benjamin Bosiak, Anna Thurmayr, Dietmar Straub
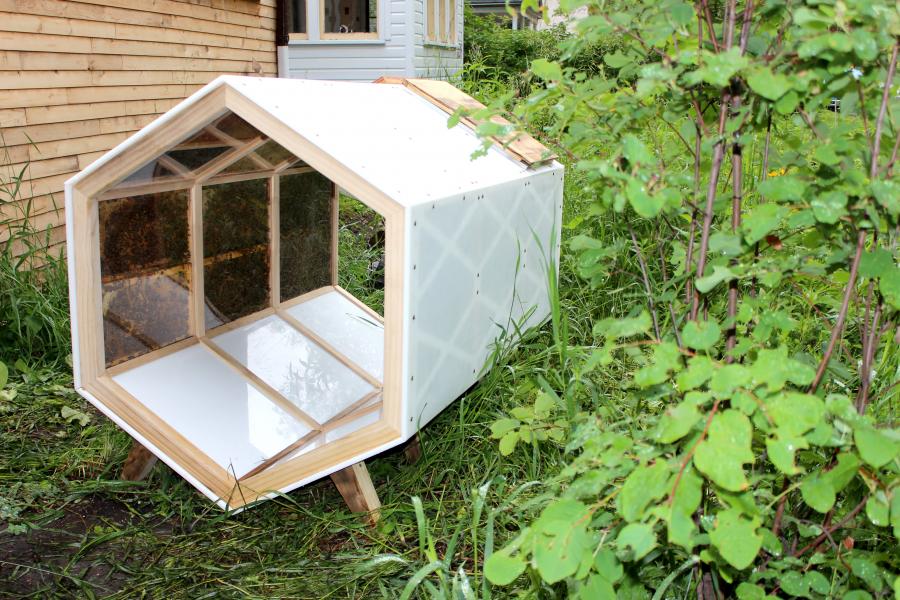
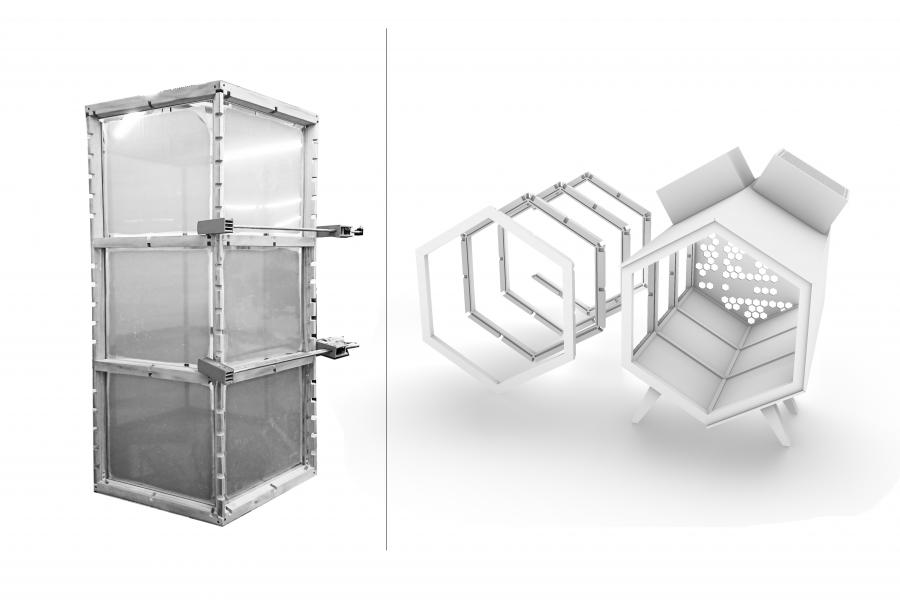
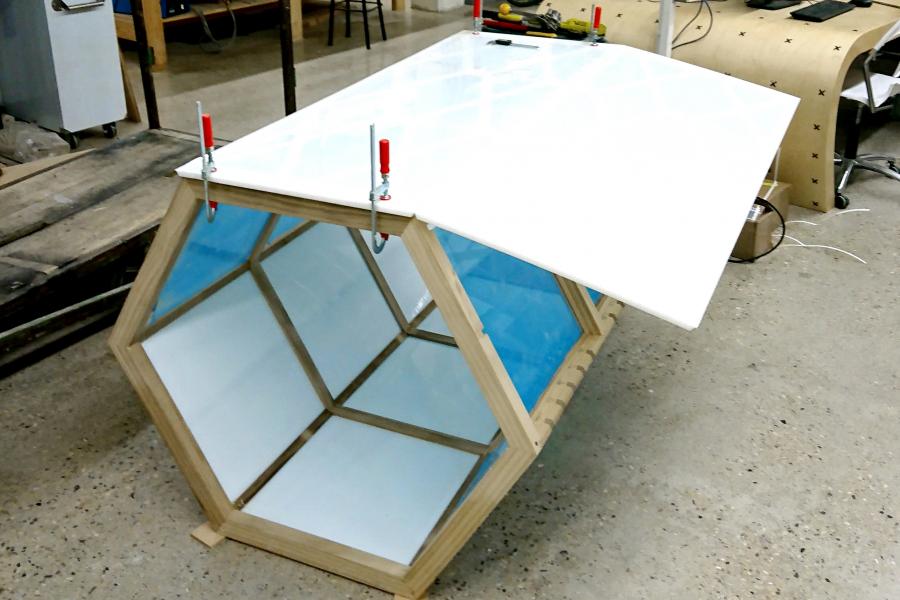
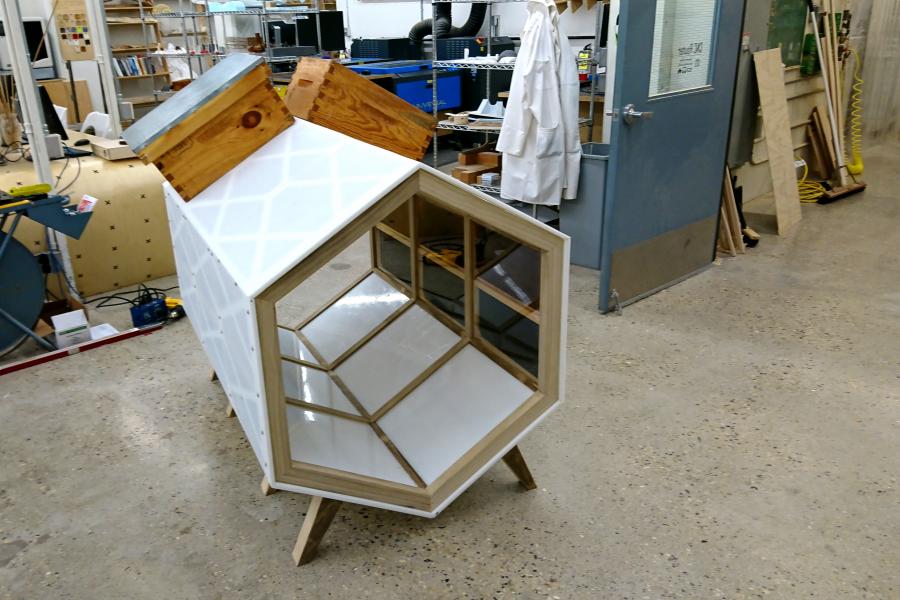
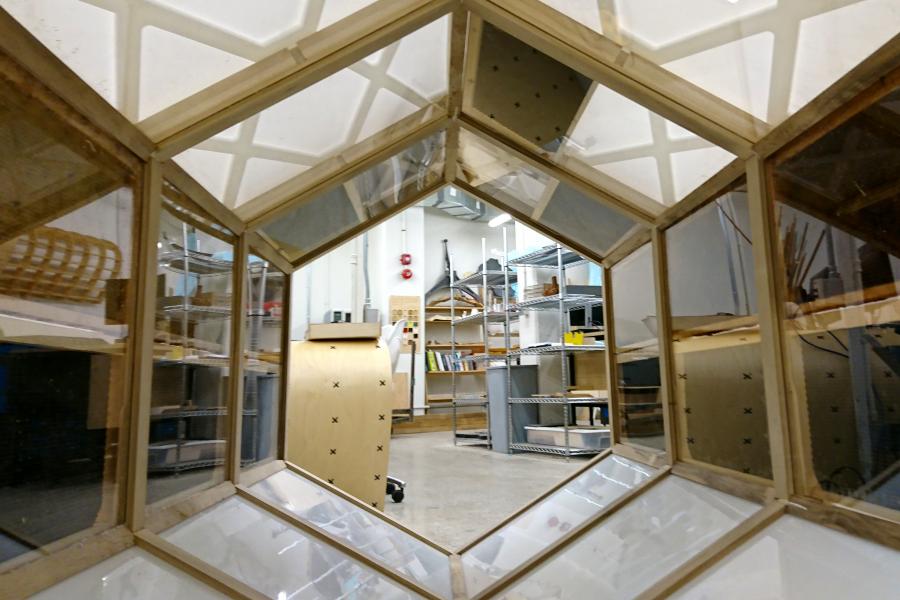